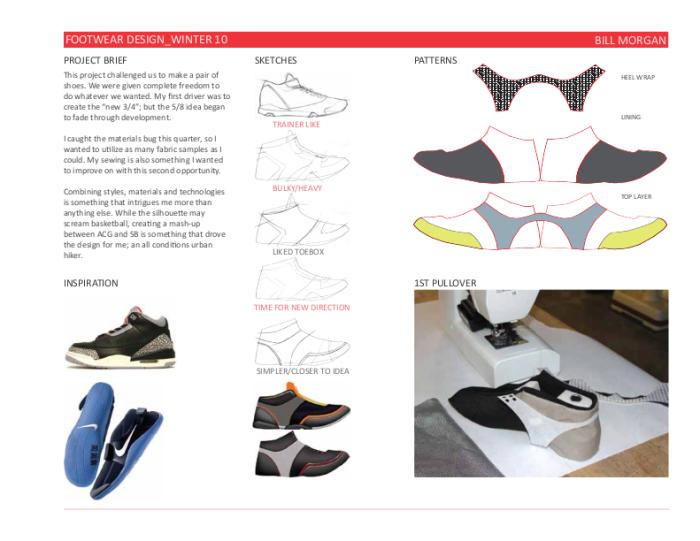
Ideation / Process - As the second project, we were asked to design and make a pair of shoes. Any size last was made available to us as well this time; so I grabbed a pair of twelves. My initial idea was to create "the new 3/4"...
A 5/8 height shoe which may bridge the gap between the two now default highs.
Sewing would also be a focal goal for me this time; I wanted to utilize the heat welder as little as possible for this project.
View PDF
View PDF
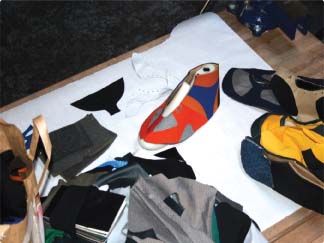
Pullover / Materials - A heat welded Knicks colorway, just to see how the pattern fit on my last. I had so much fabric that I would sew and weld pieces together just to see the results. Looking back on it now, I spendt most of the quarter Frankensteining pullovers. It was ultimately good practice sewing.
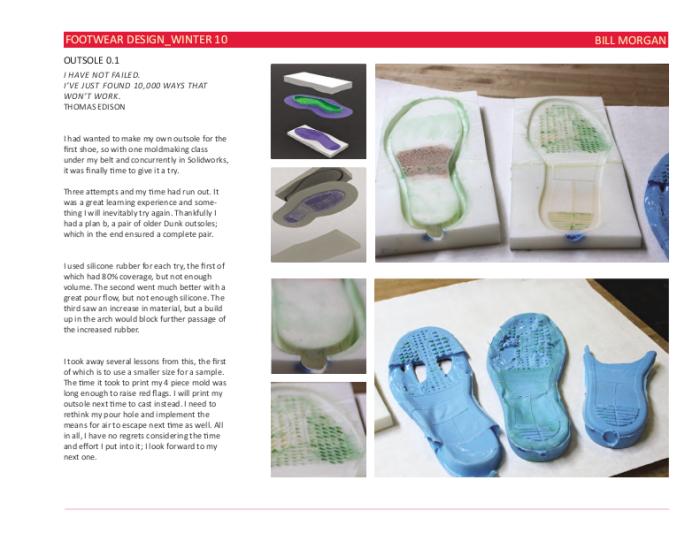
Outsole Mold - While concurrently in Solidworks that quarter, I really wanted to design and mold my own outsole for this project. My size 12 would require 4 separate pieces on the 3D printer; which I epoxied together for my 2 part mold. 3 attempts with varying results left me with no time; so I ended up removing the outsoles from a pair of old Dunks that I never wore for the final.
View PDF
View PDF
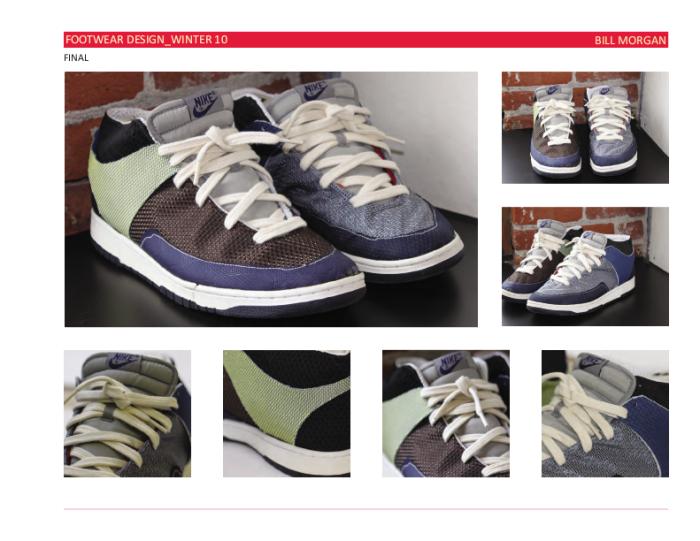
Final Sample - Like the project before it, I wanted to have contrast in materials; both in touch and visually. By then I had amassed a stockpile of sample materials, so I didn't waver in my decision of using different materials for the vamp and ankle pieces. While I was deconstructing the Dunks for my outsole, I decided to utilize the tongues as well; I felt it complemented an "old meets new" design.
View PDF
View PDF

Final uppers - The beginnings of the left shoe, with one of my outsole results. While my last fit great in it, the lug pattern underneath never filled in completely.
gLike