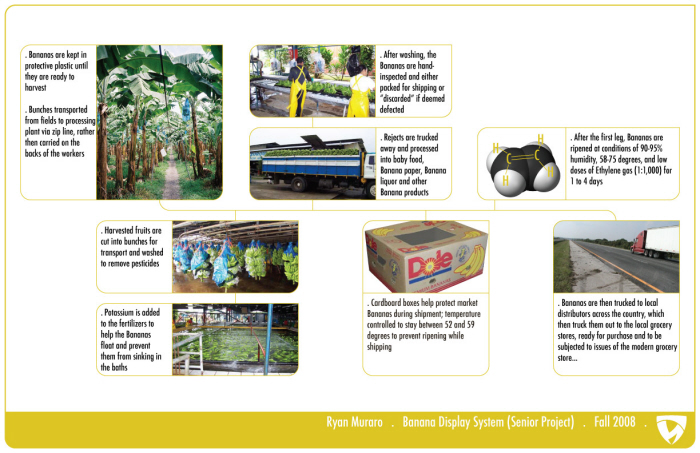
This was simply to show how companies were preventing the loss of product before it hit the shelves, and where the logic of my design fit into the existing system
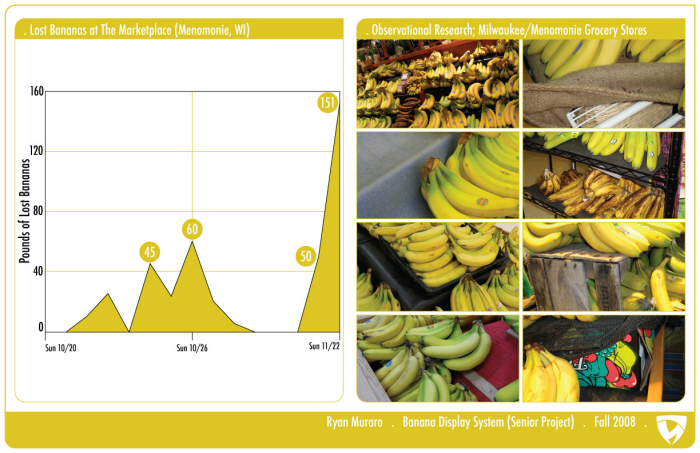
Banana Loss and Display Documentation - I was working at a Supermarket up at school while doing this project, so I retrieved data on Banana loss over a two week span (I avoided stocking Bananas during this period so it was clear the data wasn't skewed at all); The first half of my research was simply seeing other store's existing display systems and taking notes/pictures on them, 14 stores in all
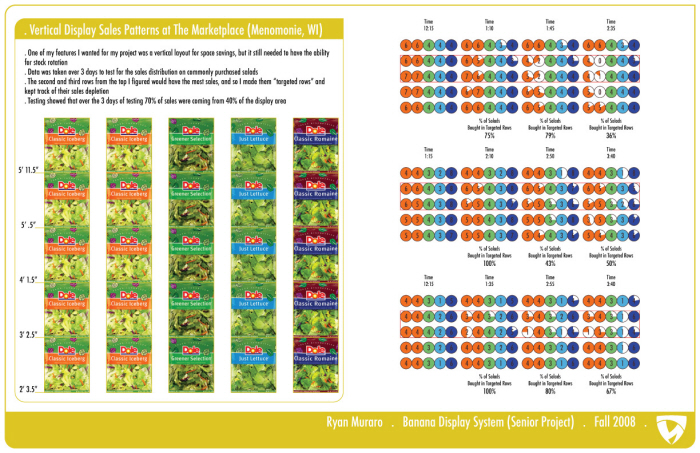
I decided on going for a vertical display to best alter the buying patterns of customers; I figured that eye-level product would sell significantly faster then product out of eye-level range, so to test this theory I arrange popular fast-selling salads on their existing displays and recorded how fast they sold. The data showed that 70% of sales were happening in 40% of the display in two rows that were closest to an average eye level (rows between 4'2" and 5'11")
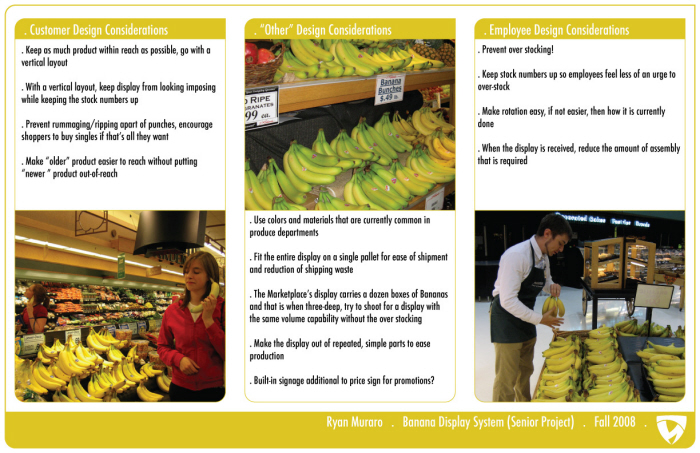
The final design had to take into account all users within the system, so I made sure to outline each group's needs to try to satisfy as many needs as possible
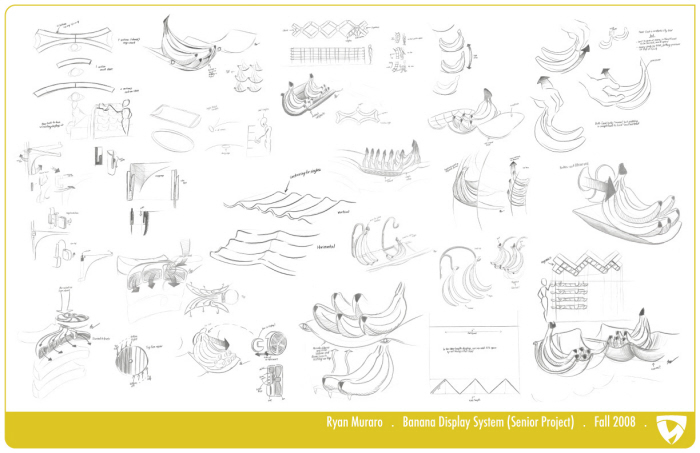
The final design was going to be a full system, so I sketched going part-by-part to create as many ideas as possible to later assemble into complete concepts
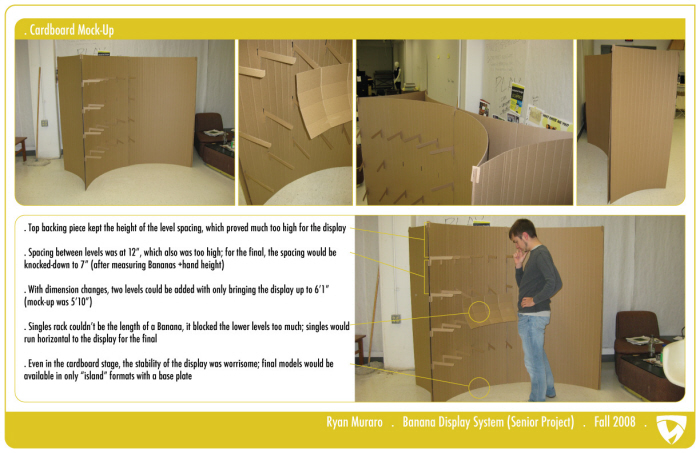
I created several fully fleshed-out concepts and from there made an initial "final" concept to build a 1:1 scale mock-up of. The dimensioning of the entire model worked much more successfully once a real life model was created to tinker with
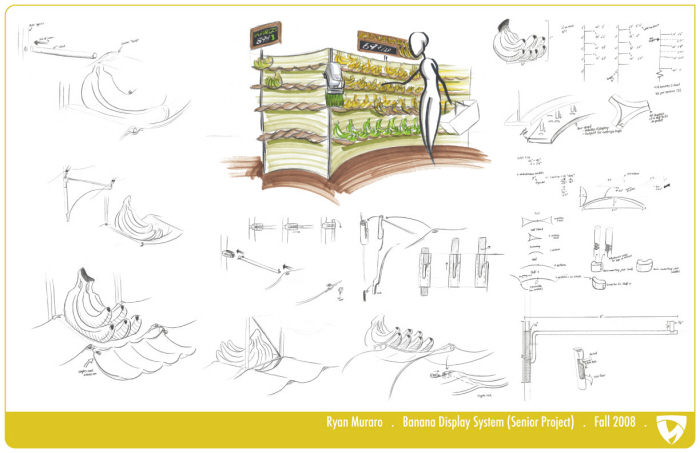
Secondary sketching, including a quick rendering of my cardboard mock-up and some of my Solidworks note-taking/on-the-fly sketching
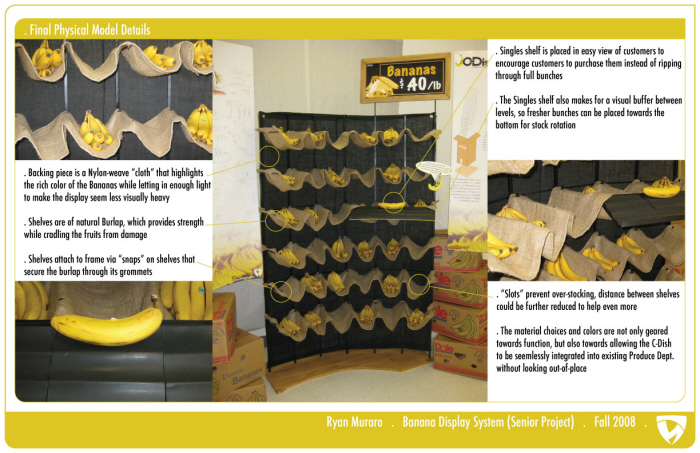
For my senior show, I decided to build a quarter-section of my display to show an idea of what my final design would be like. I also built 40 lbs of Bananas to "stock" the display, which later produced many loaves of lovely Banana Bread
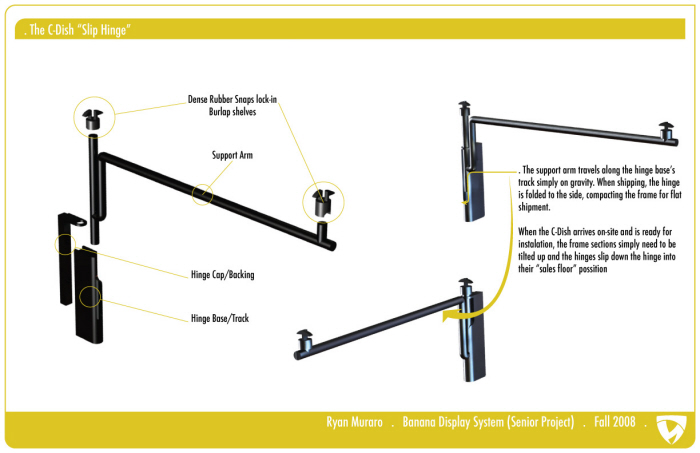
The shelves of the C-Dish had to fold flat (or detach, but that was eliminated early on due to the number of loose pieces that would create), so to ease deployment of the dozens and dozens of shelf arms I went with a locking gravity hinge; the shelf would be shipped and packed flat, then once unpacked and tilted up the hinges would fall and lock into place
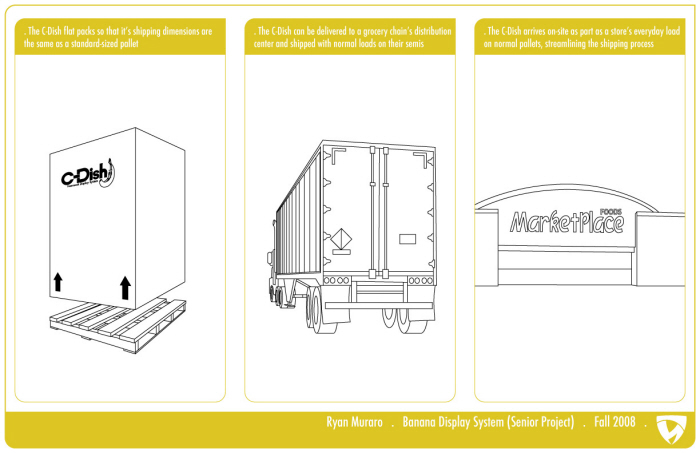
I wanted to create a system for produce departments that was as easy to implement as possible; one area in-particular was the way it was shipped. To ease shipping, the entire system packs onto a single pallet so the C-Dish (short for Cavendish, the proper name for the common Banana) can be shipped to a grocer's distribution center, where it could then be shipped to each store via the grocer's existing distribution system
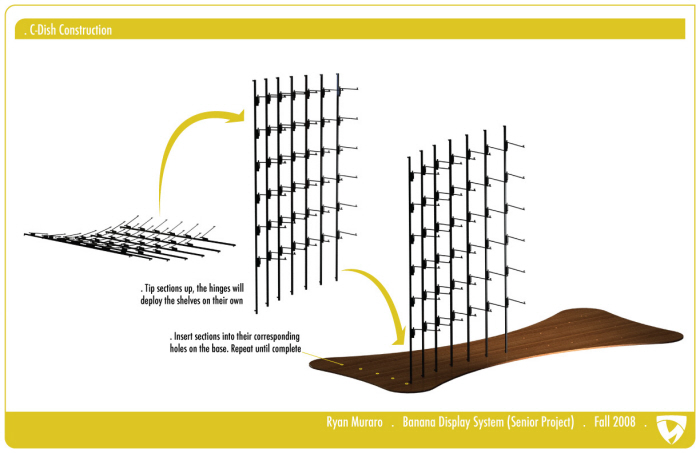
A quick overview of how the gravity-hinged shelves would deploy. The frame would be made of recycled Alluminum, the base would be made of composite veneered fiber board, and the shelving/backdrop would be made from Burlap
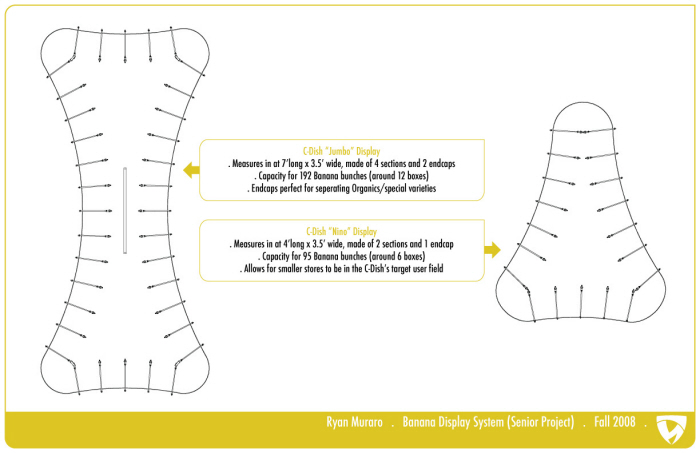
Each post on the C-Dish was identical and made of repeated elements to ease production and help create numerous display systems. I designed two separate systems, one for large stores and one for small stores; The large model was composed of 6 segments (2 ends and 4 mids), while the small "Nino" model was composed of 3 segments (1 end and 2 mids)
gLike