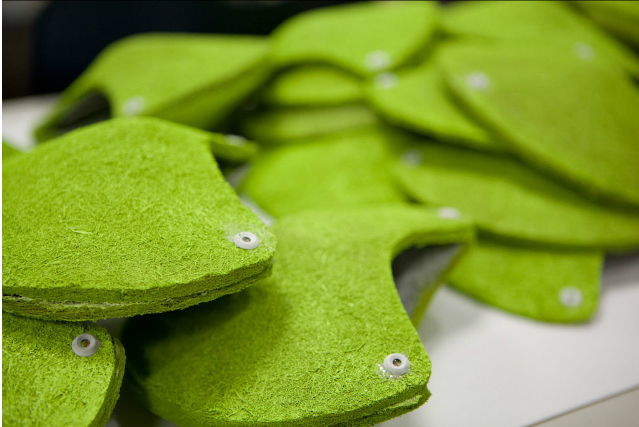
The ABEO ceiling tile is made from jute, a highly absorbent material that can be heated and pressed into this unique shape. The tile has three different connection points from which it can hang or be attached to other tiles. The tiles can create many interesting shapes to fit in any unique space.
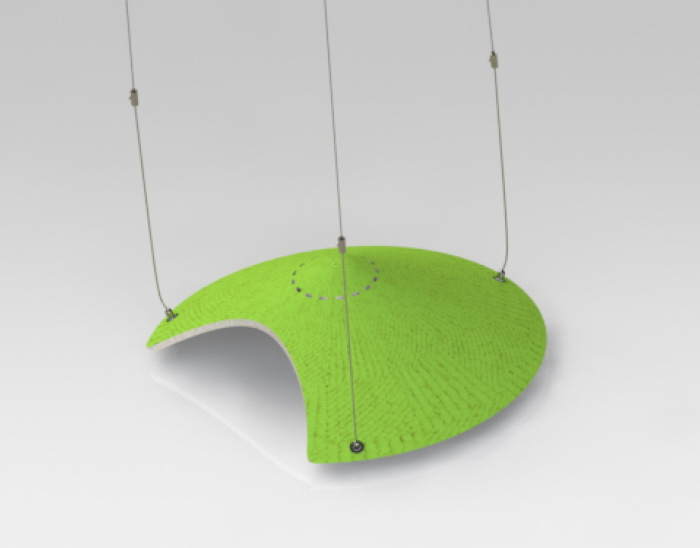
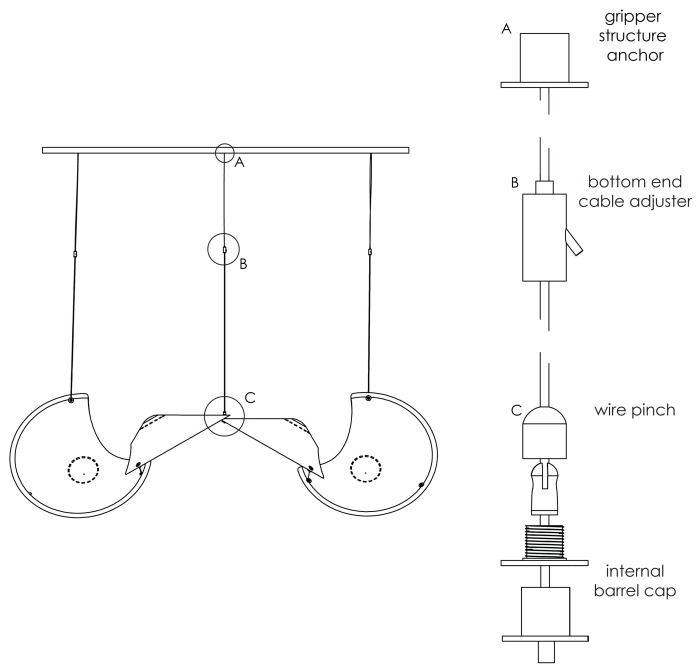
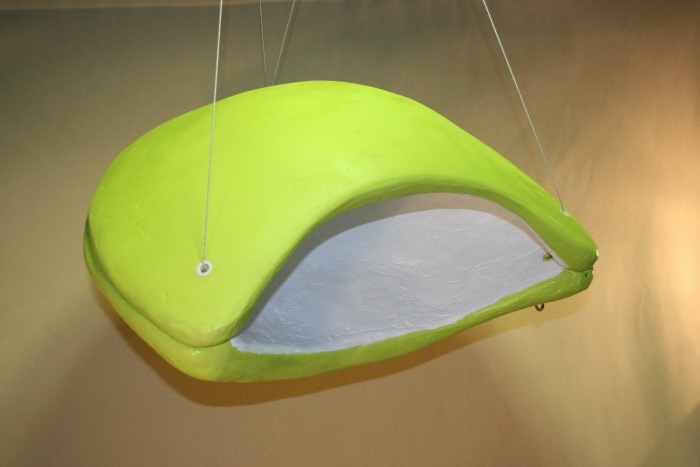
Full-scale model (blue foam, spackle, spot putty, and paint)
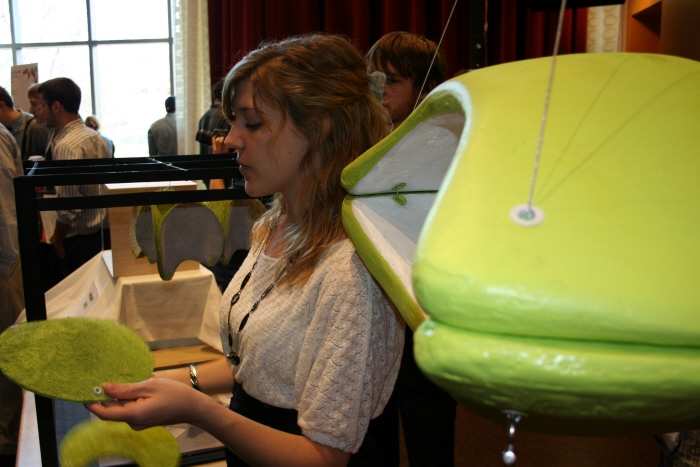
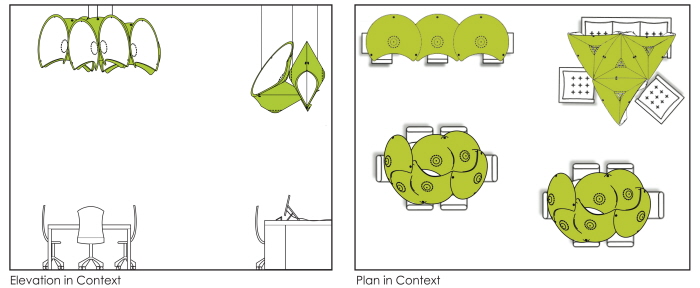
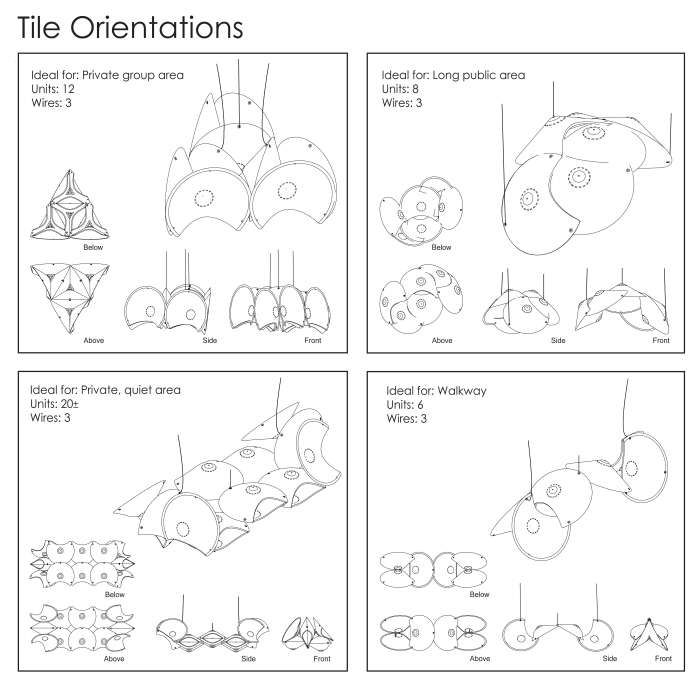
My team and I designed a few specific configurations of the ABEO tile for different settings.
This configuration is ideal for the ceiling above a group meeting space, for example, group tables in a university library. The interior tiles form shells that trap sound coming from that area, while the exterior shells reflect noise coming from the surrounding area.
This configuration is ideal for the space above a quiet area such as a row of computers or private work areas. The tiles form shells facing outward to catch the sound coming from the surrounding area, keeping the space below quiet for concentrating students.
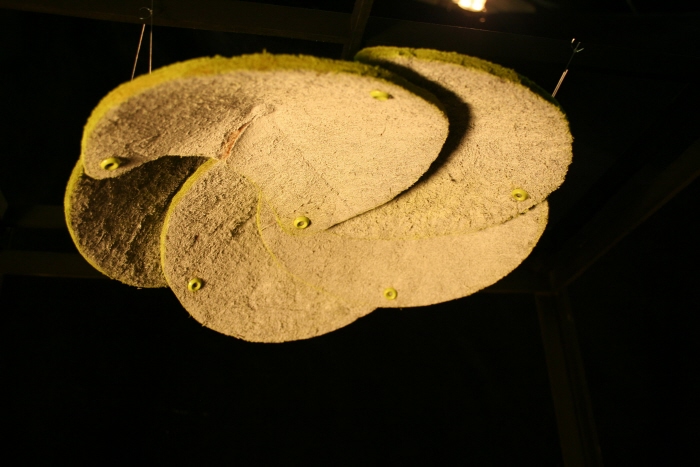
My team and I made several quarter-scale jute models to aid in the design of the different configurations.
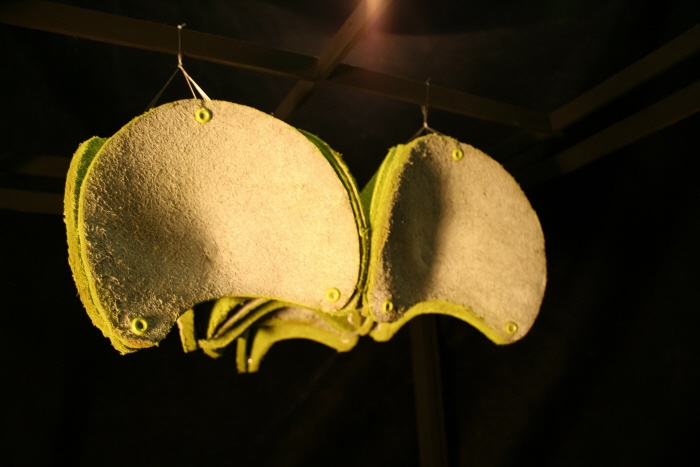
My team and I made several quarter-scale jute models to aid in the design of the different configurations.
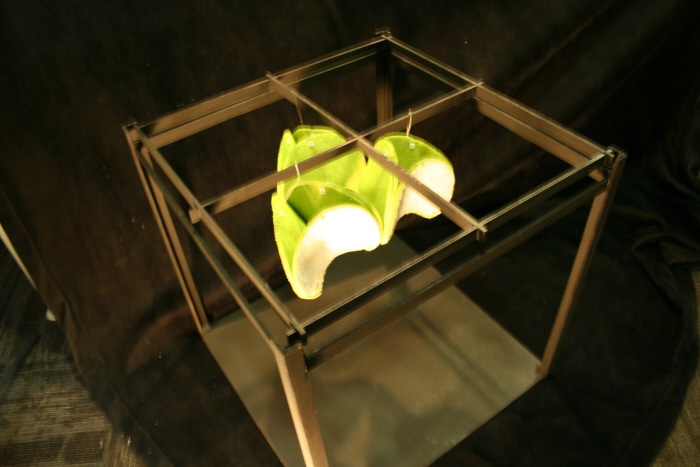
For the final presentation we used this frame with interchangeable tops to present each different quarter-scale, jute model configuration.
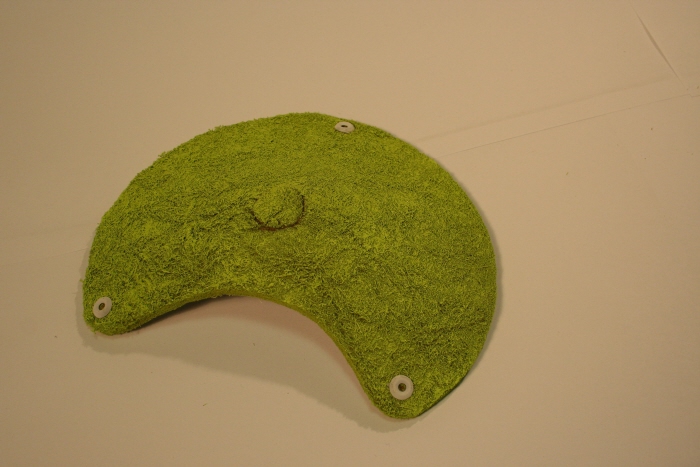
A perpherated circle is cut into each of the ABEO tiles and can be popped out to allow for the installation of commercial light.
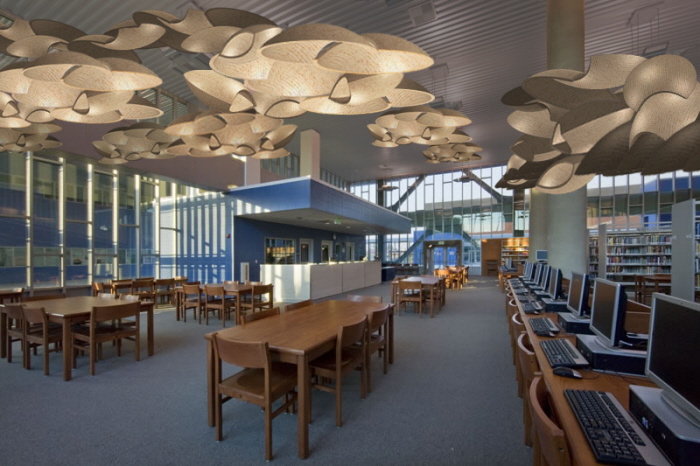
A rendering of our ideas halfway through the week, before we landed on the specific ABEO shape
We made MANY quarter-scale jute models
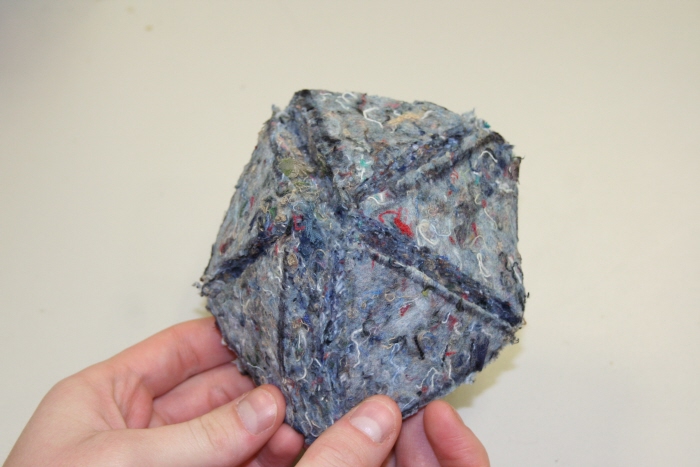
We tried a variety of different materials from the sample of acoustic materials donated to us by Armstrong. Cutting, shaping, dying and heating to experiment.
We first discovered the malleability of jute after trying to heat up and form many different sample materials given to us by Armstrong. The jute was easy to cut without causing fraying and held its shape when heated up and held around a mold.
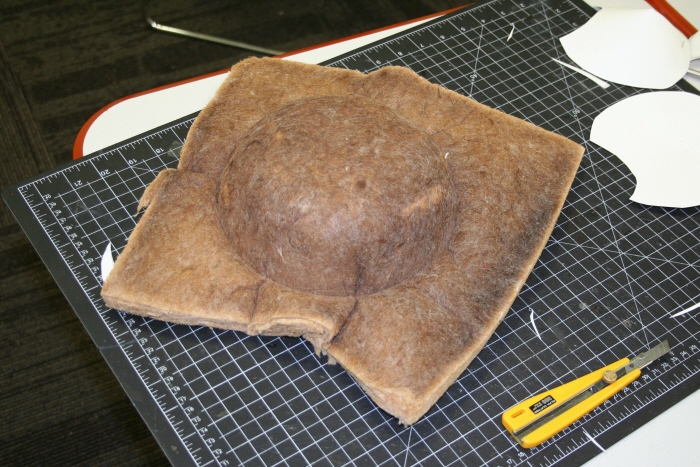
For our quarter-scale models we heated the jute up on our shop's vacuum-former.
We build a mold to place the heated jute in to create the exact unique shape we wanted each ABEO tile to have.
After pressing the jute in the mold for about 60 seconds we had our quarter-scale ABEO tile!
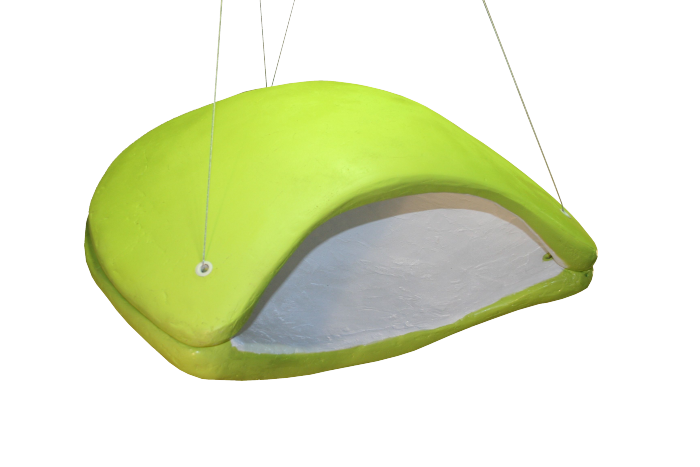
The completed full-scale models that we built, formed into a shell and hung by each of the three connection points of the top shell.
After discovering the ABEO shape, we made many paper models to test out the configurations we had in mind.
After discovering the ABEO shape, we made many paper models to test out the configurations we had in mind.
After discovering the ABEO shape, we made many paper models to test out the configurations we had in mind.
After discovering the ABEO shape, we made many paper models to test out the configurations we had in mind.
After discovering the ABEO shape, we made many paper models to test out the configurations we had in mind.
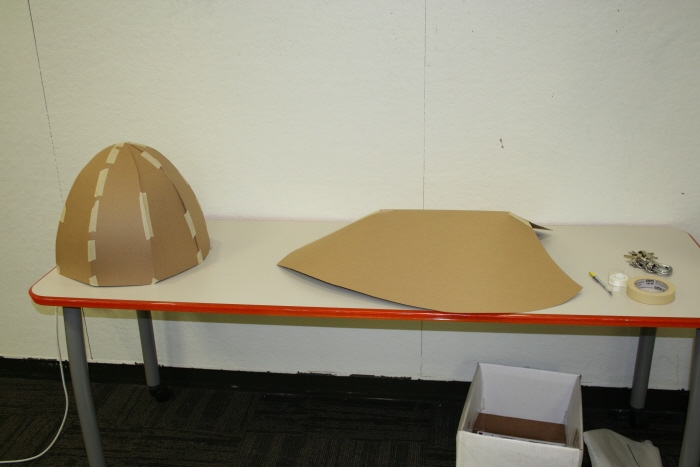
Moving from quarter-scale to full-scale we tested out the shape with chip board to test out the width and exact shape that we wanted for the ABEO tile.
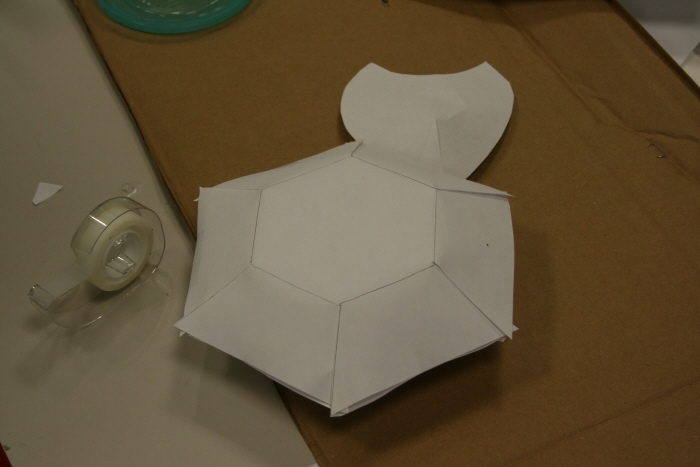
It took quite a few paper tests to find the right shape for the ABEO tile.
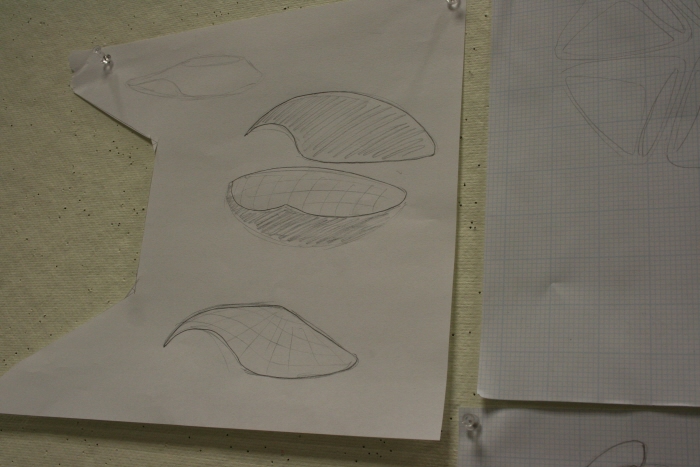
A shell shape with an opening was the idea we liked most, it could reflect sound on one side and capture it on the other. It could easily come together with other tiles in many different ways.
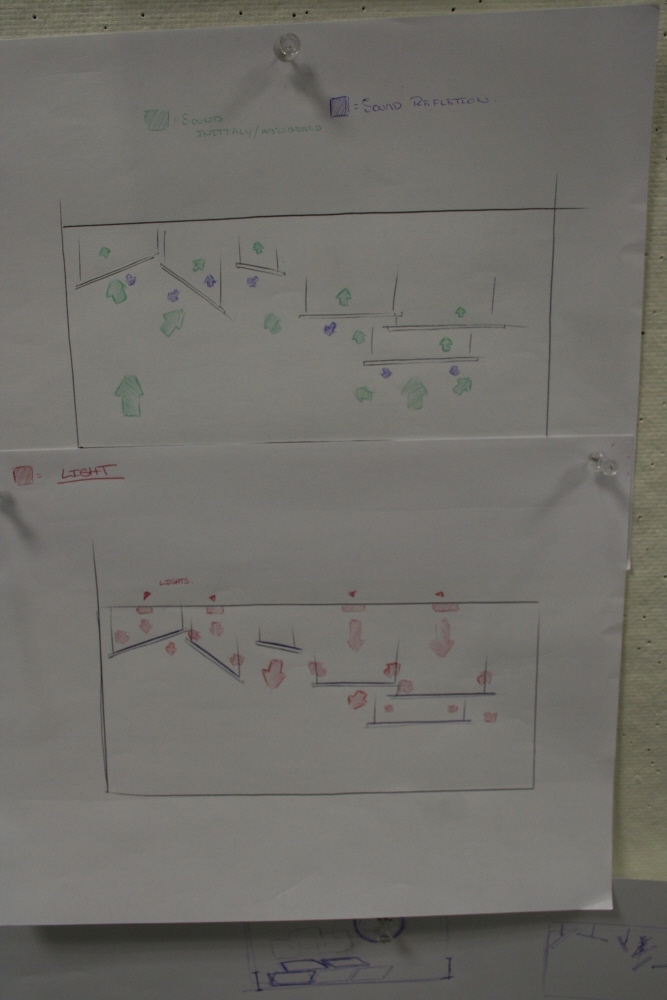
When deciding what shape to make the tile we took a great deal of consideration into how the tiles might be configured throughout the room.
My devoted team and I. Although we didn't know each other at the beginning of the challenge we were good friends by the final critique at the end of the week.
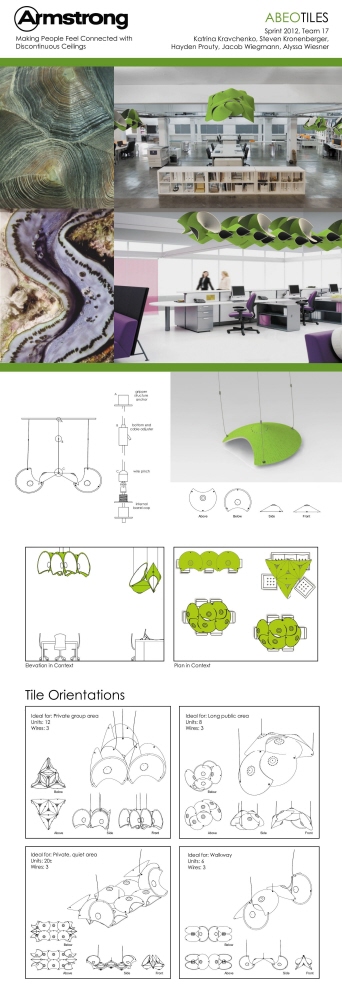
The final presentation board for the ABEO discontinuous ceiling tile.
View PDF
View PDF
gLike