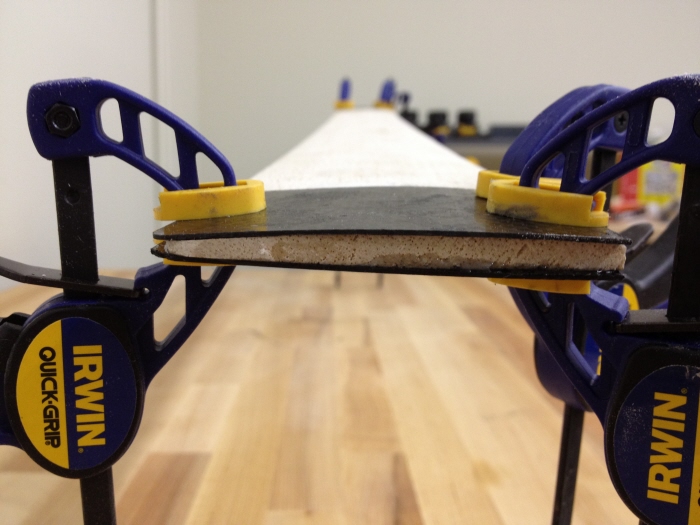
Our wings were made of balsa wood. A piece of carbon fiber was attached to each of the wings' inner end, in order to make the pivot point link stronger.
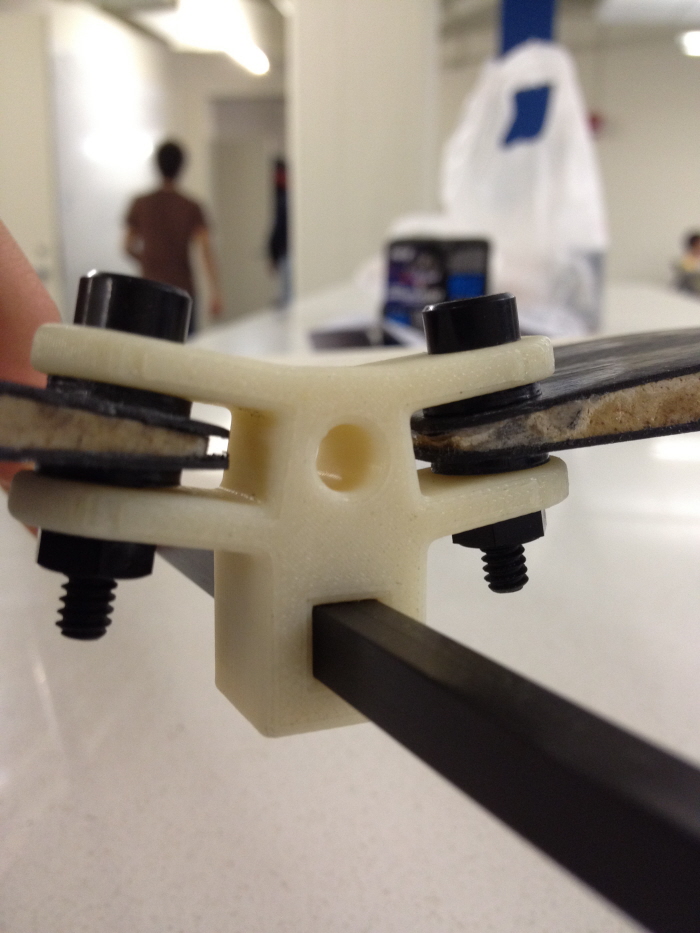
We designed and 3D Printed a piece that would work as a pivot for both wings. The middle hole was included such that rubber bands could go through it with the purpose of pulling open the wings for deployment.
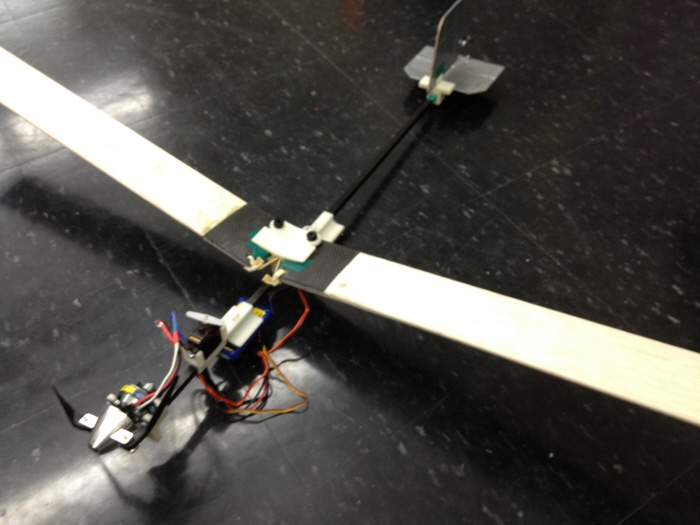
The first prototype of "El Pitirre" consisted of a carbon fiber hollow bar as the body, two wings that folded inwards and were then pulled open by the elastic force of rubber bands. A rudder and elevator, made of cardboard covered in duck tape, were controlled with two separate servos. Every "holder" part was 3D printed and could slide along the body bar in order to adjust the center of gravity of the plane.
Problems: The wing area to weight ratio was too small and thus the plane didn't have enough lift. We needed to either increase the wing area or decrease the plane's weight.
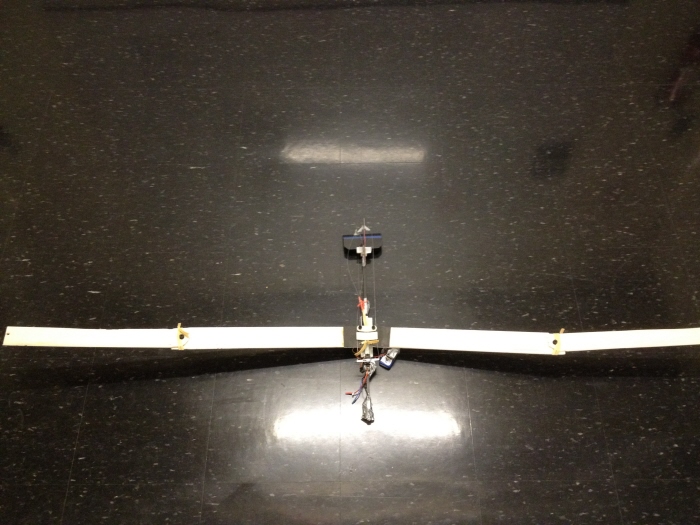
El Pitirre: Prototype 2.
In order to address the wing area problem, we double the length of each wing.
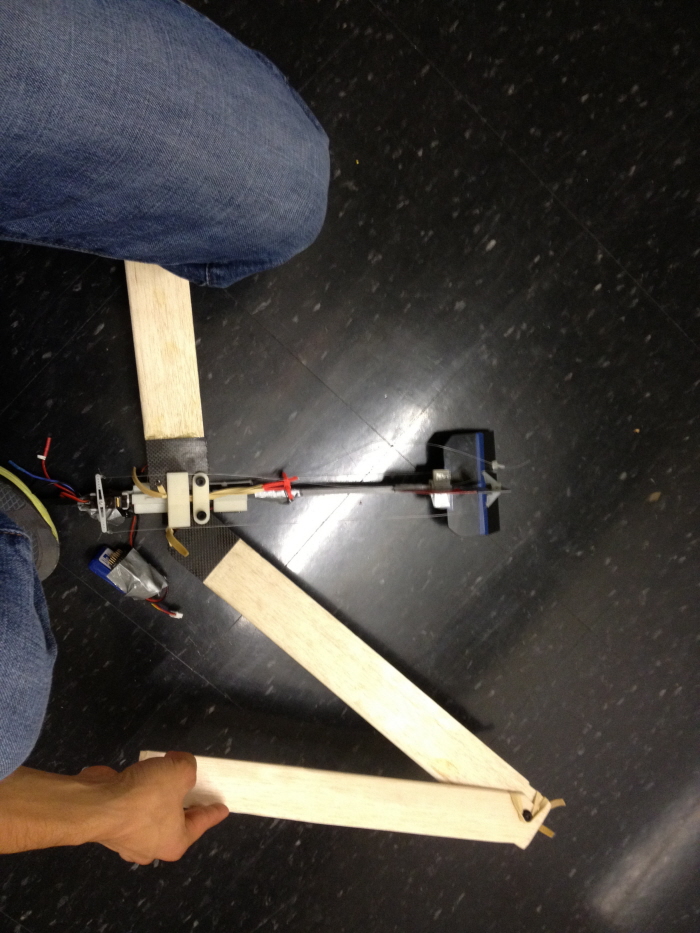
Doubling the length of each wing showed new problems. The original rubber bands method didn't result as an efficient way of fully opening the wings to a straight line as desired.
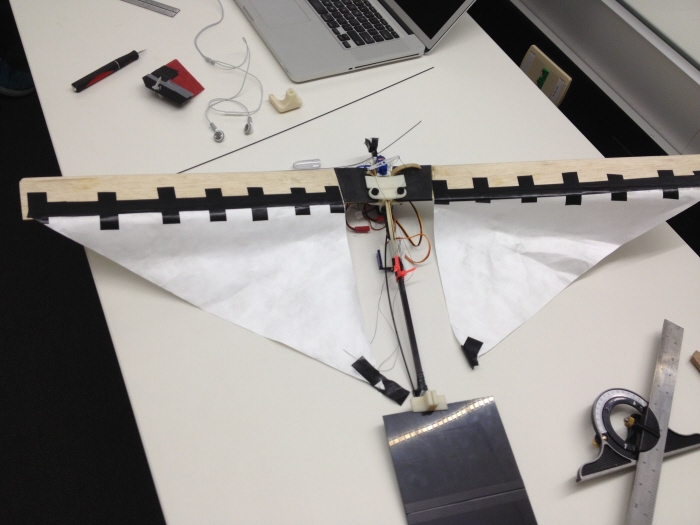
El Pitirre: Prototype 3.
In order to increase the wing area while keeping the added weight at a minimum, we decided to add paper to the back of each wing. We also modified the rudder and elevator to carbon fiber pieces instead of cardboard and duck tape. This change allowed those pieces to be more rigid and less heavy.
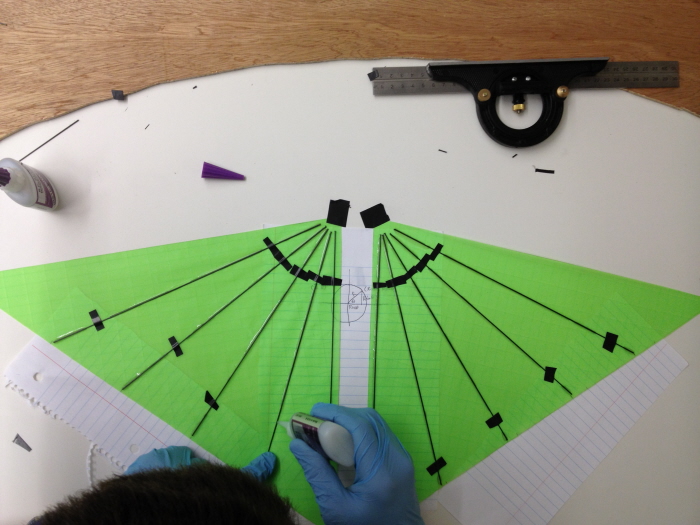
The paper wings showed positive results, but they kept getting wrinkled and eventually torned due to the repetitive folding and unfolding of the wings. We changed materials from paper to nylon and also added ribs to the wings to add rigidity. We also chose a pretty awesome color.
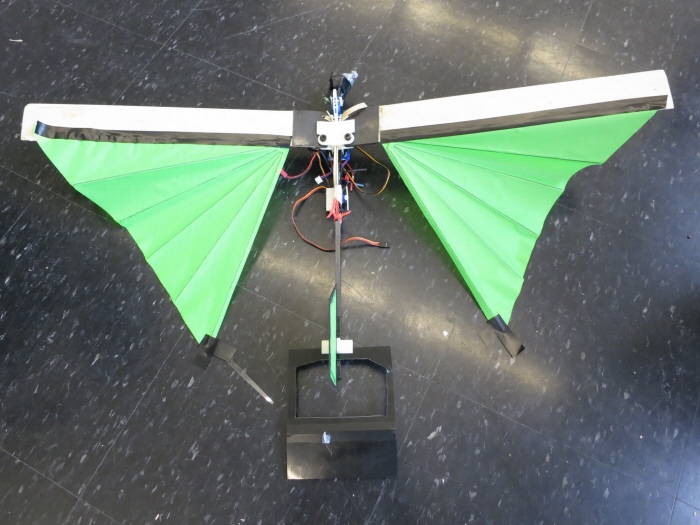
Final prototype of El Pitirre.
As final modifications to the plane, we removed the inner section of the rudder and elevator and covered those holes with nylon with the purpose of removing final bits of weight.
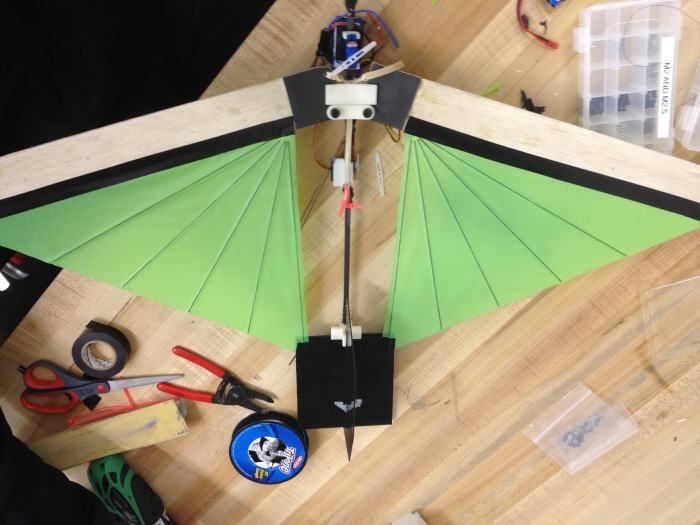
El Pitirre, Version 2,374. Ready to fly!
gLike