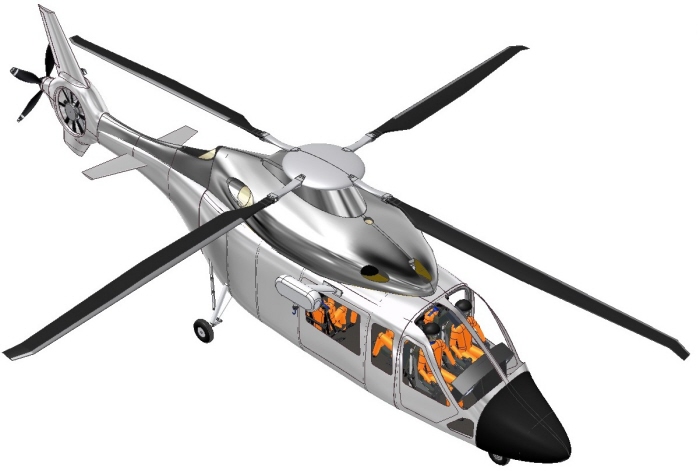
Velocicopter was tasked with performing 3 missions: search and rescue, insertion and re-supply. Given the specific requirements for each mission, the critical mission requirement was the range and time frame given for the search and rescue mission.
In order to achieve the designated goal, the helicopter had to maintain a constant speed between 193 and 270 knots for 50-70 min. In order to achieve this, it was necessary to use thrust compounding, which led to the proposal seen here.
This is a 3 engine design, where the third engine is used only to power a propeller at the rear of the helicopter during "super cruise". In order to engage the third engine to the drive train of the helicopter a slip clutch was used.
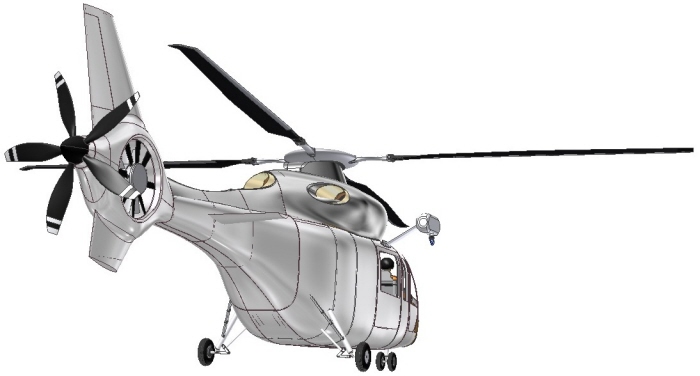
Velocicopter Specifications
Maximum speed: 235 knots
Maximum cruise altitude: 7000 ft
Empty weight: 5512 lb
Base price: $7.61 million
Operating cost: $1500 / hour
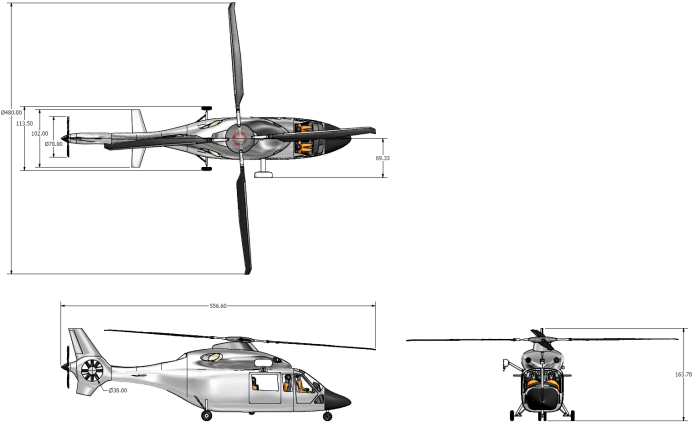
Dimensions of helicopter in inches.
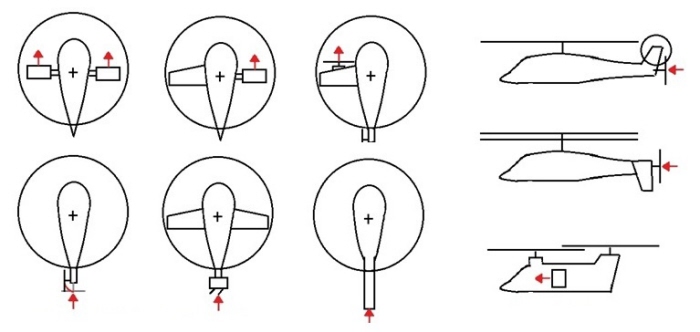
Several options of compounding were evaluated before determining the final configuration for the design.

The initial steps in the determination of the layout for the helicopter were to determine the passenger cabin layouts necessary to achieve the missions assigned to the aircraft.
This image shows the cabin layouts for the search and rescue mission.
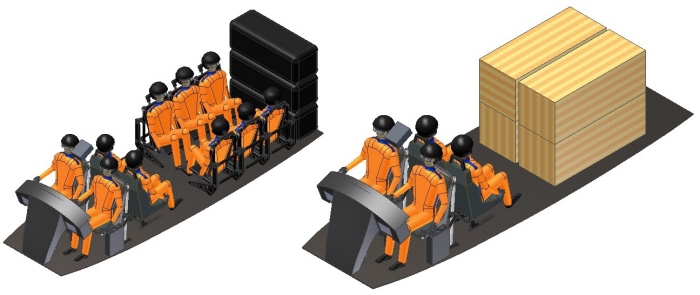
Cabin layouts for insertion (left) and re-supply missions.
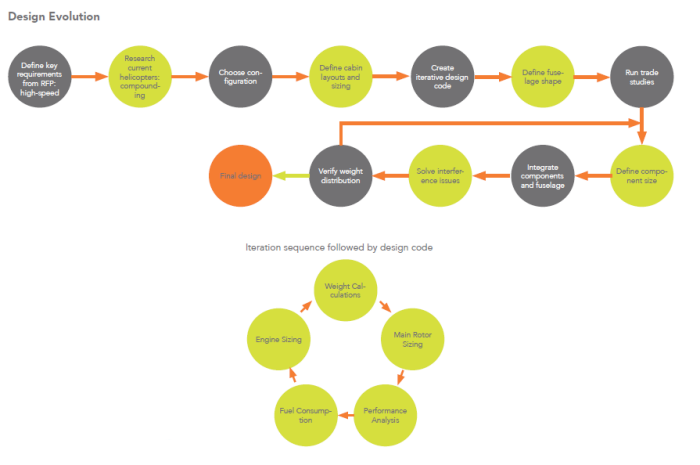
Sizing of the different components of the helicopter and their location were iterated using a design code created by the team.
This image shows the design evolution of the project and iteration sequence followed.
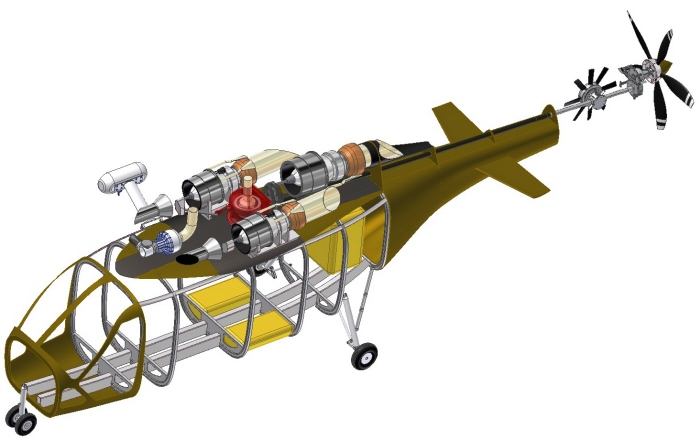
The main structure of the helicopter was then created around the cabin designs.
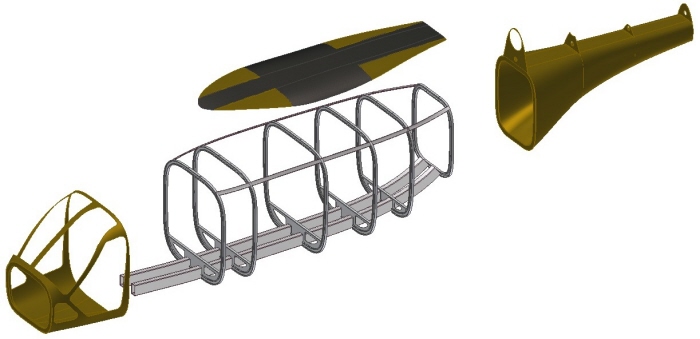
The main structure of the helicopter was designed in a modular manner, combining PEEK/Kevlar monocoque structures and aluminum-lithium bulkheads and keel beams.
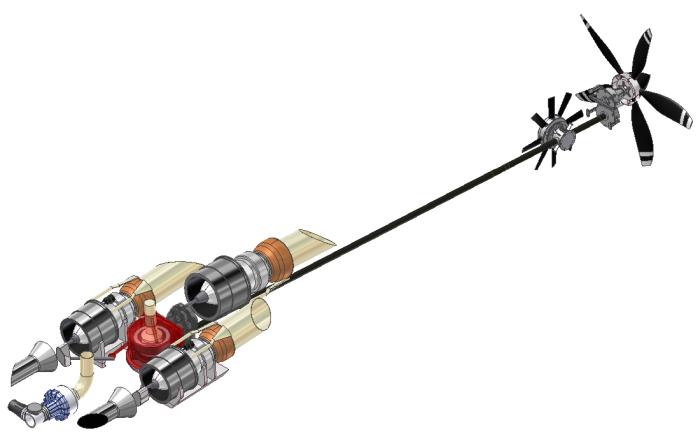
The propulsion system used two 745 HP engines to power the main rotor and fenestron and a single 2550 HP engine to power an auxiliary propeller used for "super cruise". Additionally an APU was used for engine start-up.
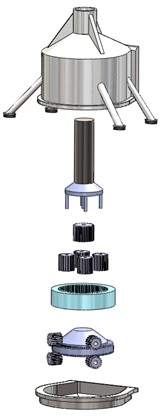
This image shows the main planetary gearbox used to move the main rotor and fenestron. It is designed to handle single engine failure.
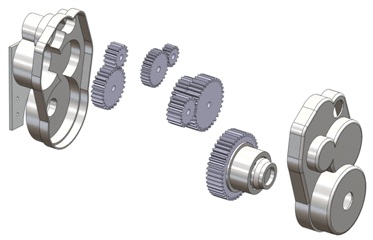
Auxiliary gearbox is used to power auxiliary propeller through a slip clutch mechanism.
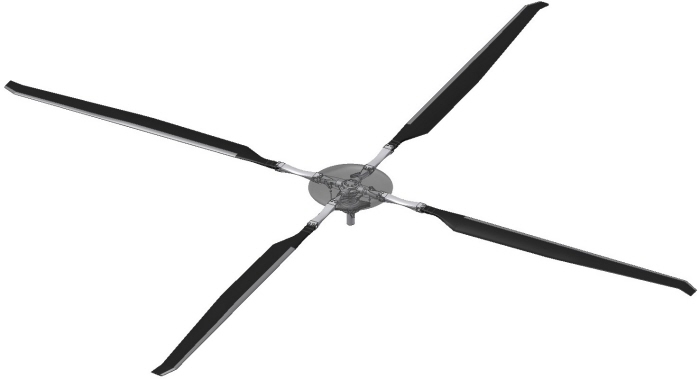
The helicopter main rotor is 40ft in diameter and uses four blades made from carbon fiber spars and nomex cores. It employs swept tips for noise reduction.
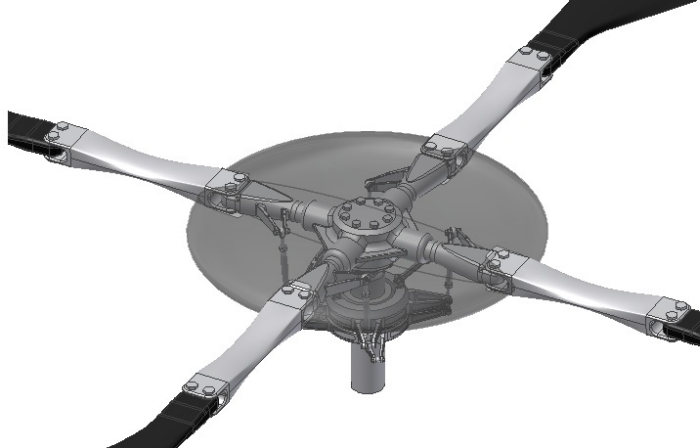
The main rotor hub is hingeless, utilizing virtual hinges to allow for flap. Hub cover is designed to reduce drag.
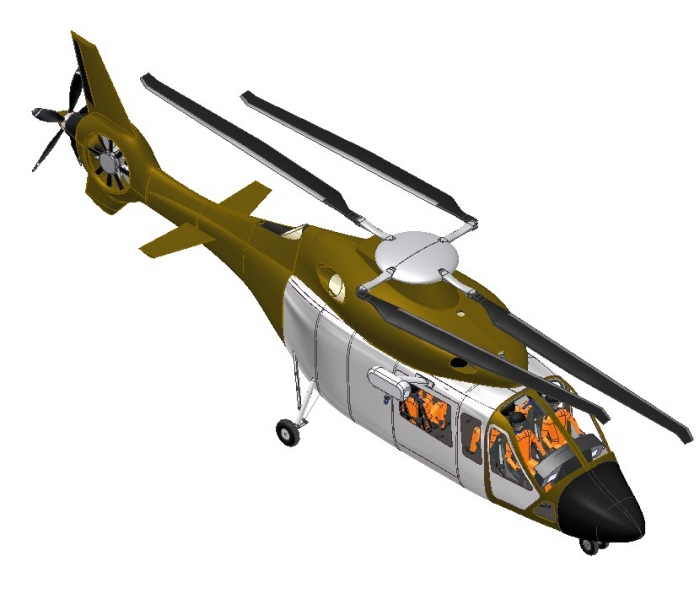
Main rotor blades are foldable to allow for ship-based operation.
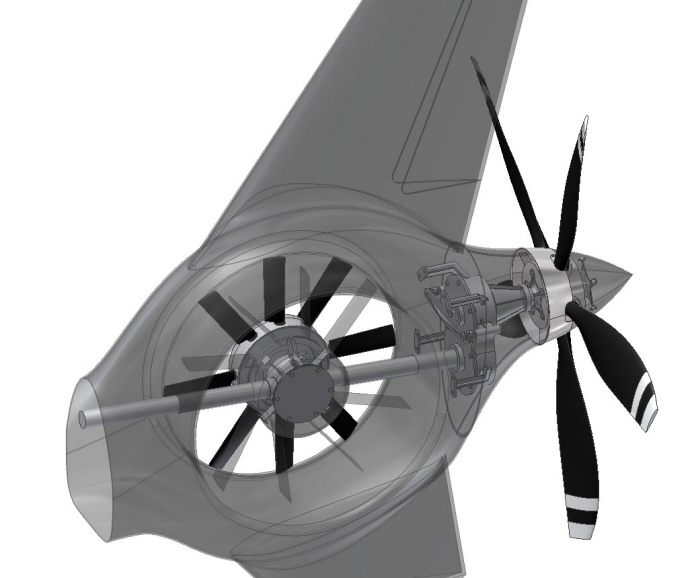
Fenestron is 38 inches in diameter and provides 822lbs of thrust using 8 blades @ 5500 rpm. It includes a variable blade pitch control mechanism to control thrust. It is offloaded completely by vertical tail at cruise speeds.
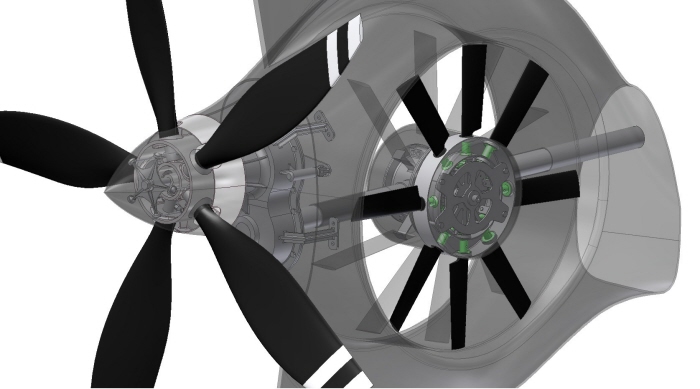
Auxiliar propeller is 78" in diameter. It uses 5 blades producing 1800 lbs of thrust @2535 rpm. It also includes a blade pitch control mechanism to control the amount of thrust produced. It only provides thrust during "super cruise".
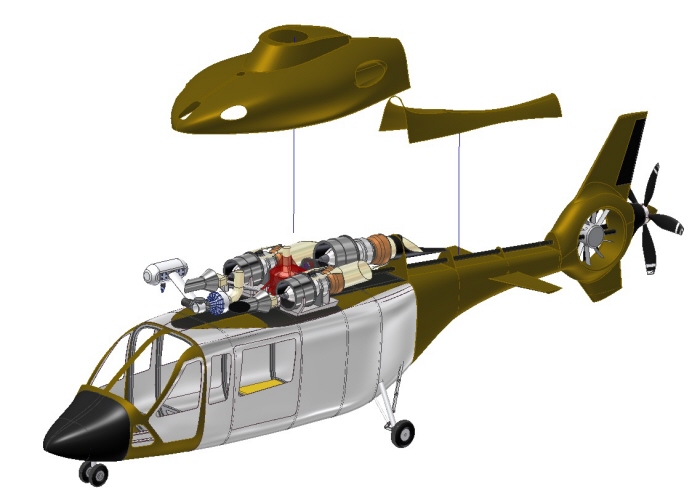
Composite cowlings are used to encase the mechanical components of the helicopter.
gLike