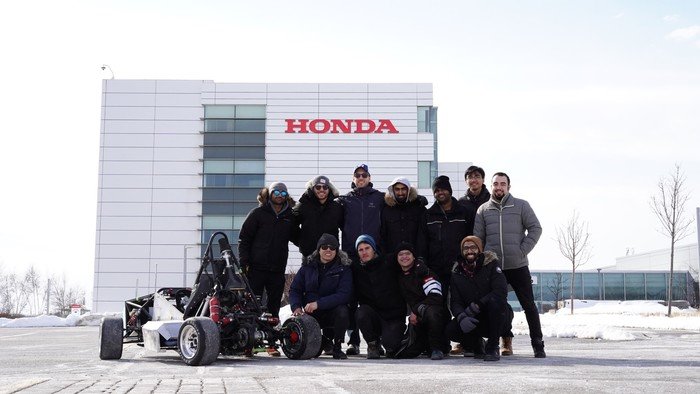
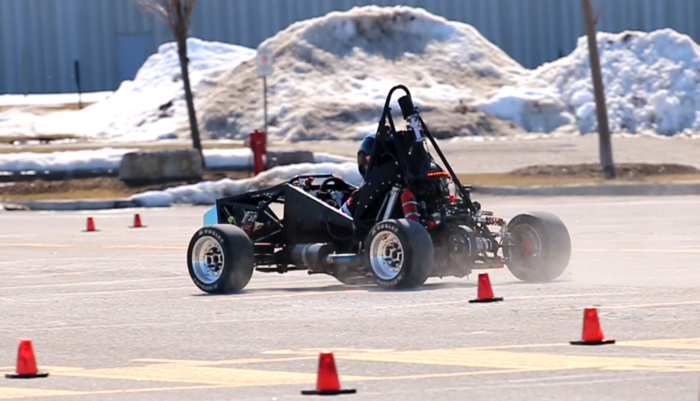
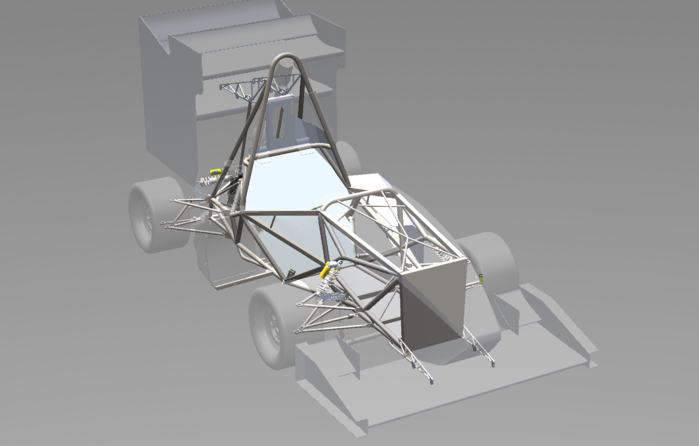
The car assembly, with the non-transparent items being either designed by me completely or with direct involvement. This included:
- Frame - the design was for the meeting of strict safety regulations. It then also had to meet manufacturing limitations of the tube bending and cutting supplier, and packaging of driver, electrical, and suspension.
- Suspension arms and damper linkage geometry (primarily rear). Also jigged and welded them.
- Sheet metal - Firewall, upper firewall/headrest support, fuel splash shield, main floor, front floor. Also guided the design of the exhaust shroud. These were all made of 3003 aluminum, 1/16 and 1/32, and sent by me to lasercutting.
- Wing mountings - plate steel initially (and square tubes in the rear) and later cut out of 6061. The design was based on my concept from the previous year, and the analysis (topology, Solidworks FEA) I helped perform.
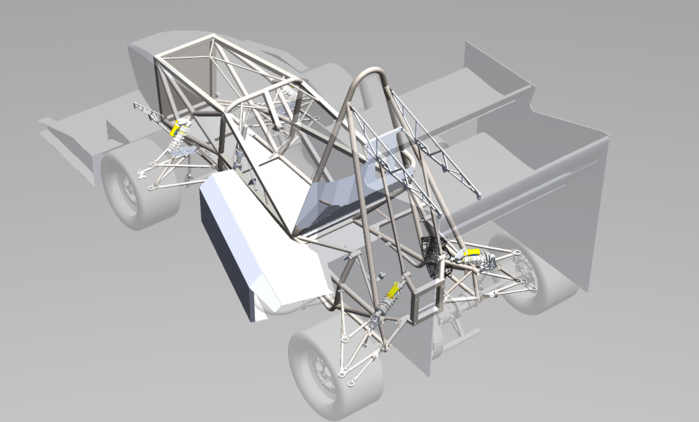
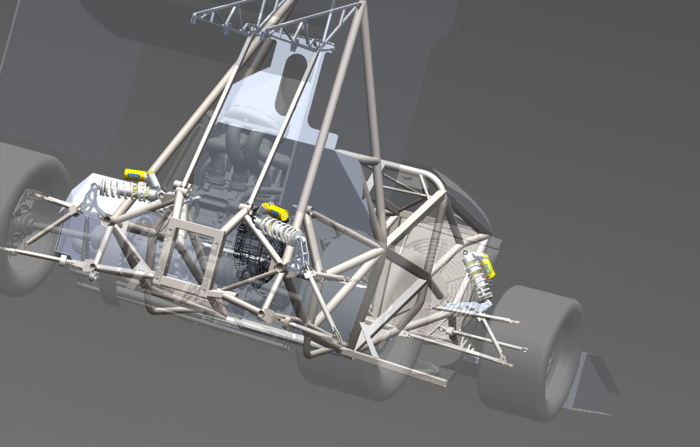
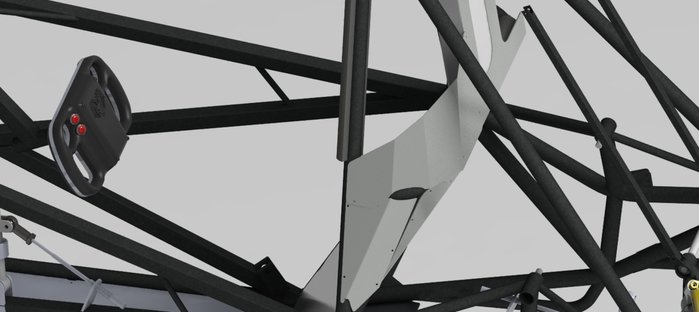
Apart from the tube-frame, I was also responsible for the safety paneling. That included the firewall, floors, and headrest plate. In this picture the firewall and headrest plate are seen, as well as 2 additional panels that were put in to be on the safe side of the regulations, preventing any fuel spray.
They were lasercut (etched bends) and bent manually on the brake press - 3003 Aluminum (it was easy to work with, low strenght inconsequential - and given for free), 1/16 and 1/32 thickness.

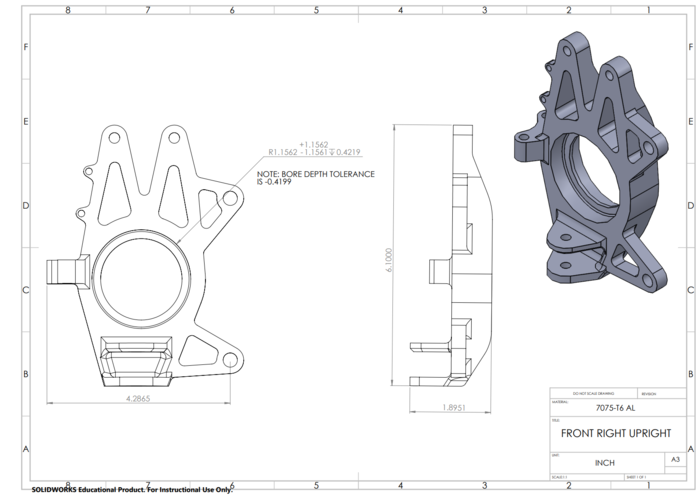
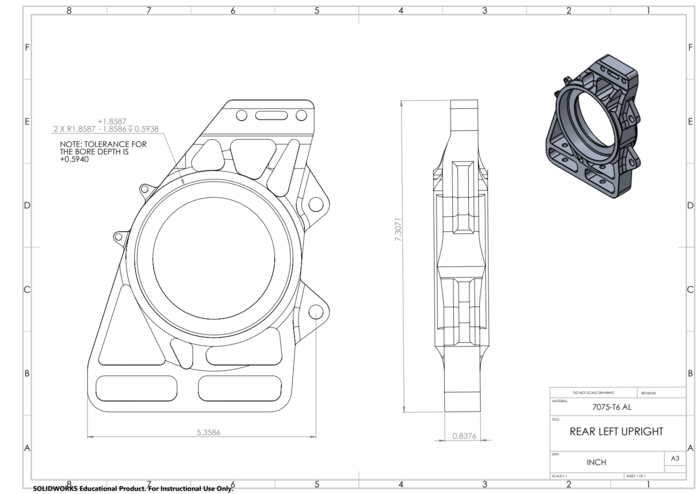
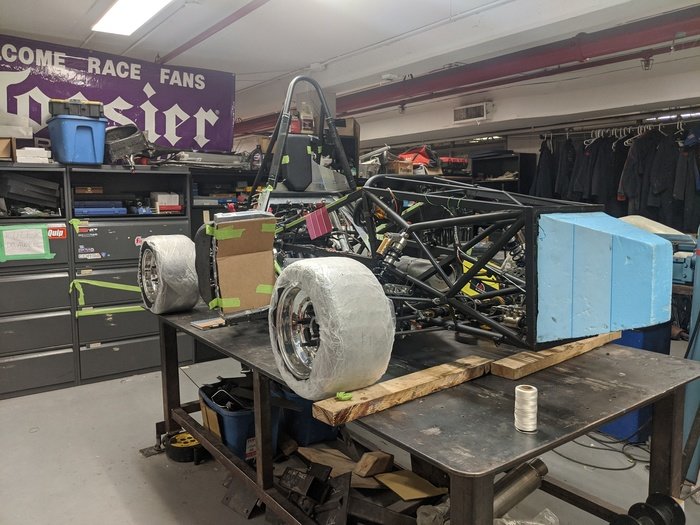
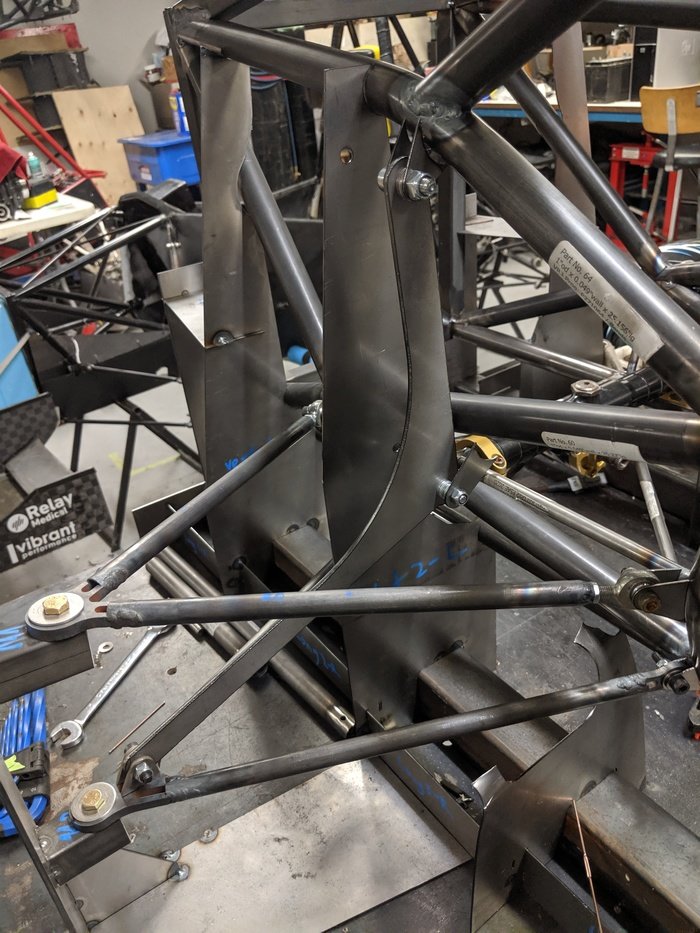
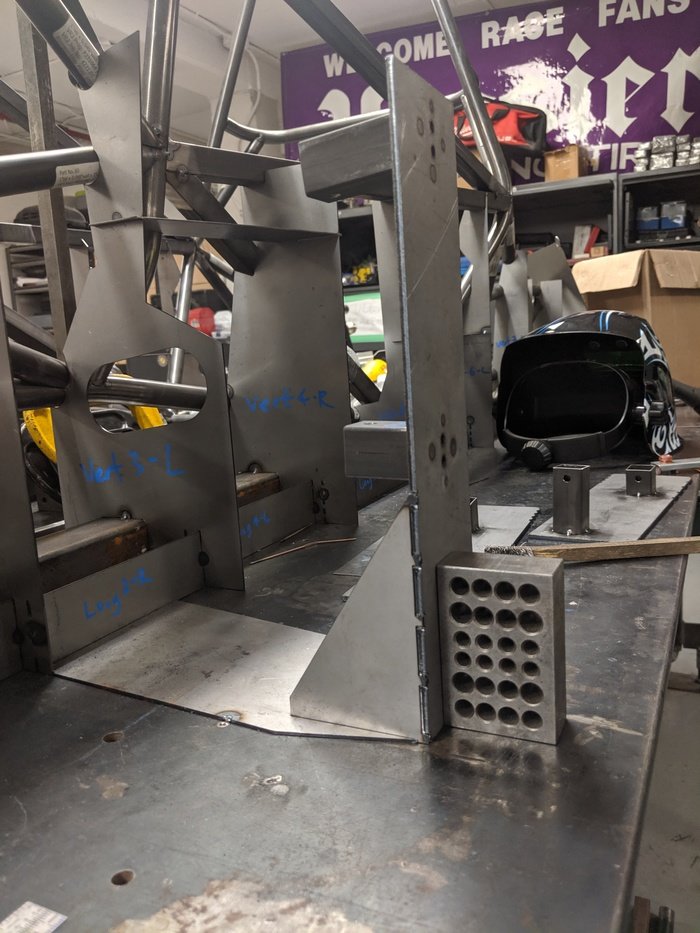
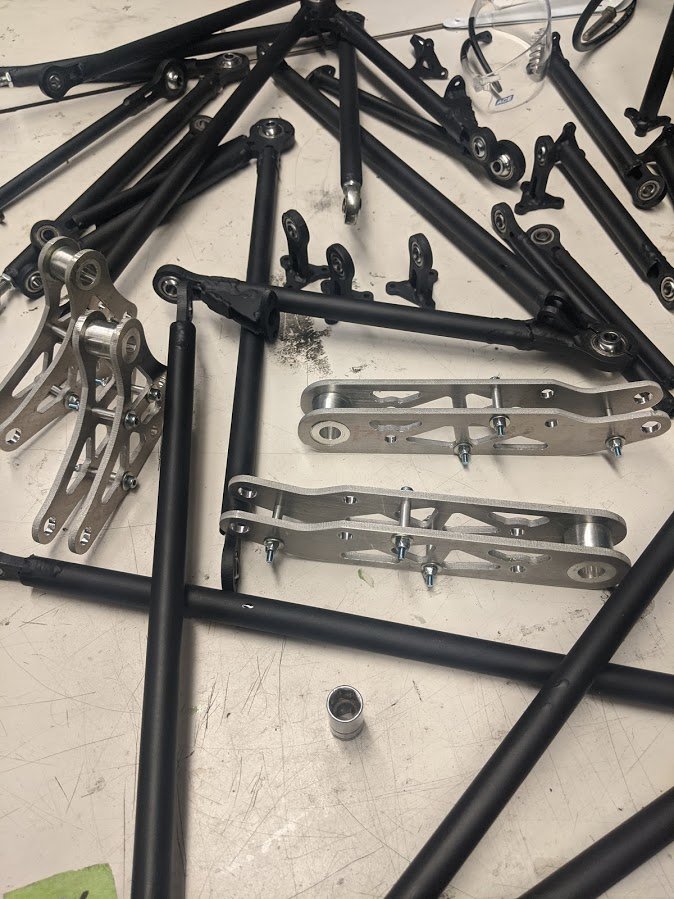
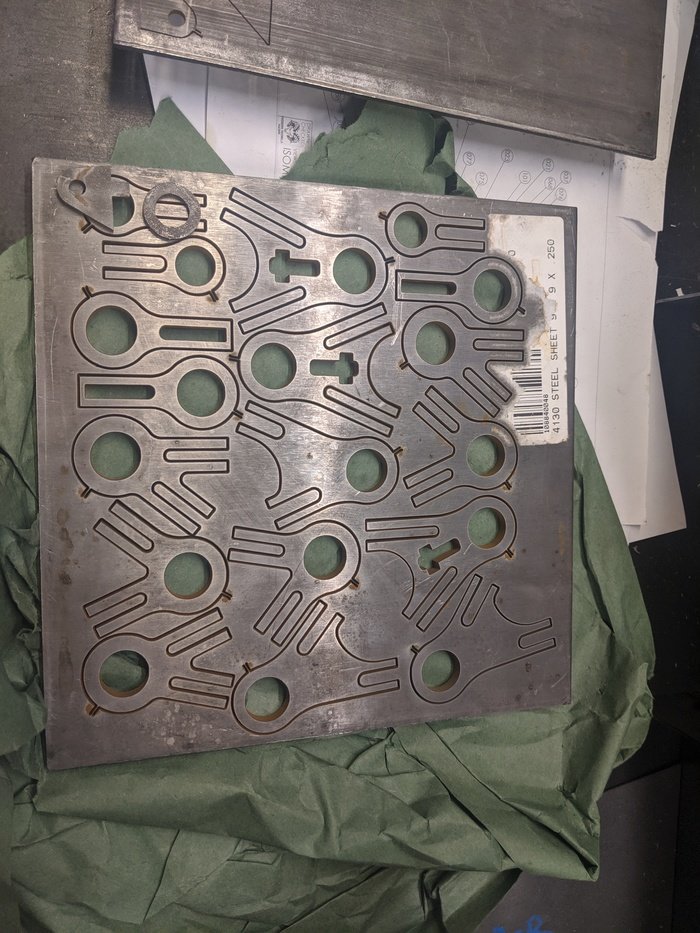
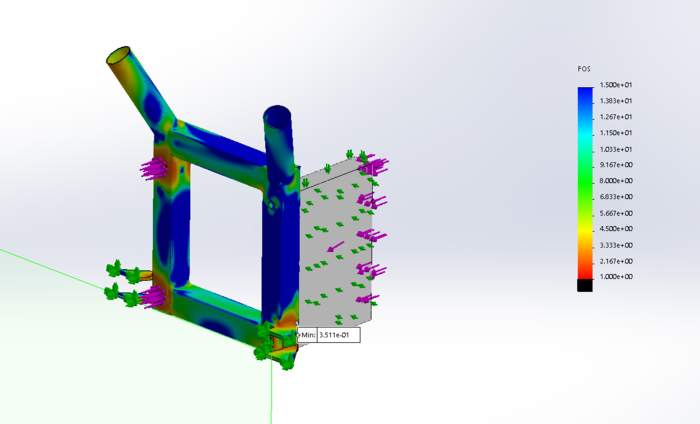
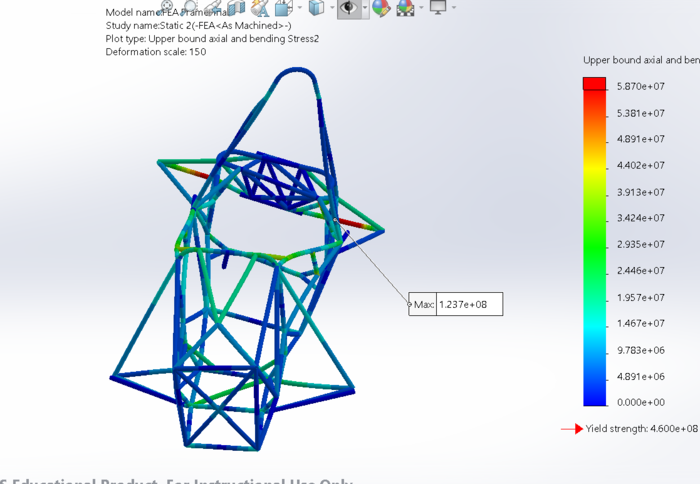
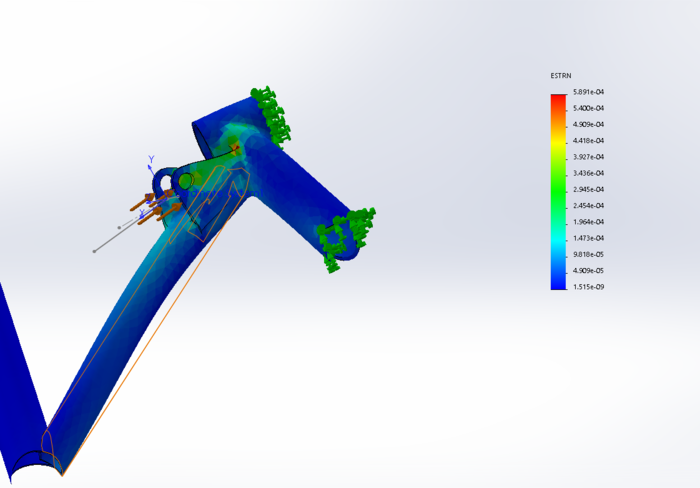
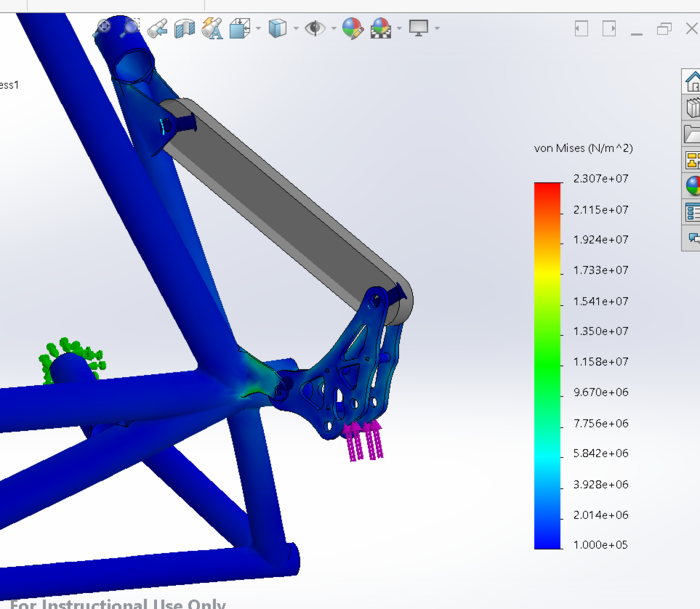
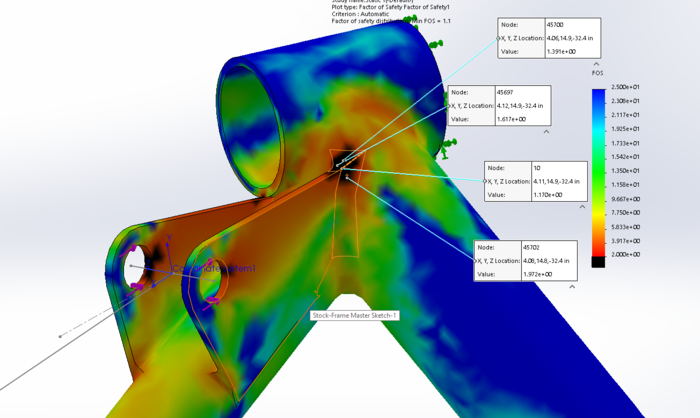
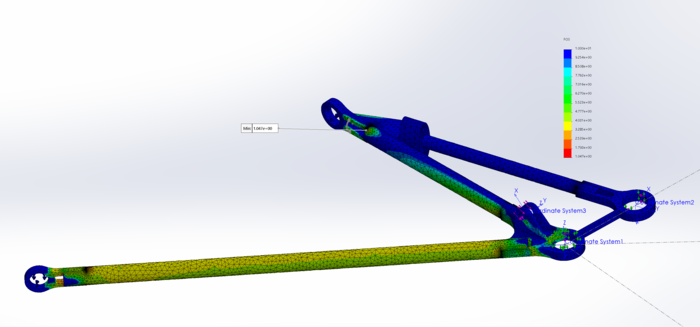
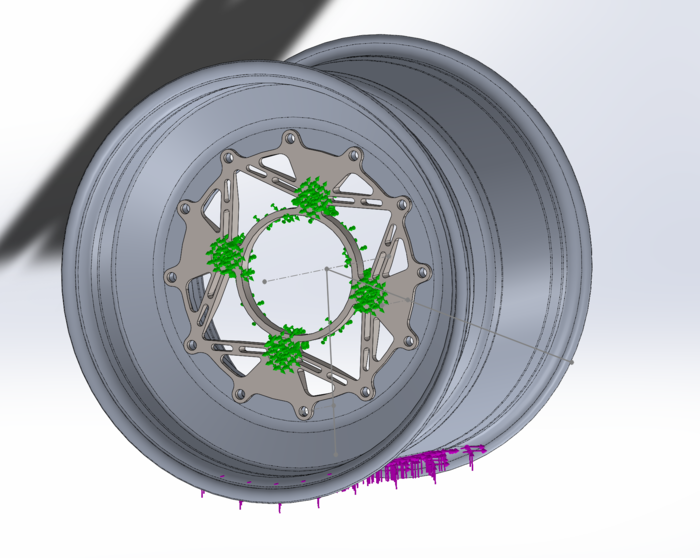
A "wheel center" for the chosen rim shells - 3 piece design. This was to be made of titanium. We decided to shelve the project, as budget was tight and the titanium sponsorship did not come through.
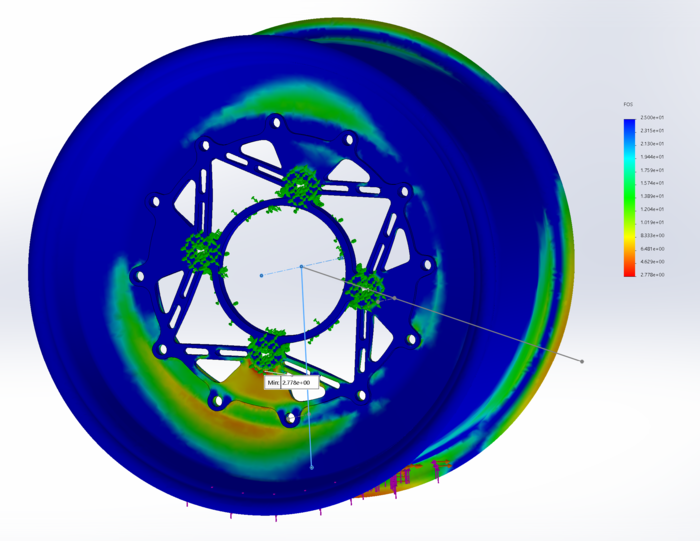
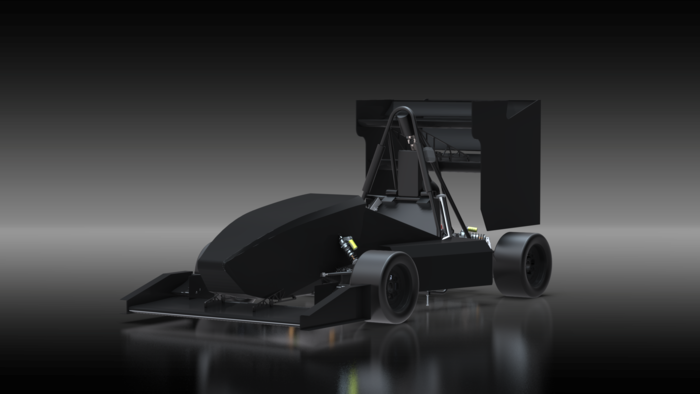
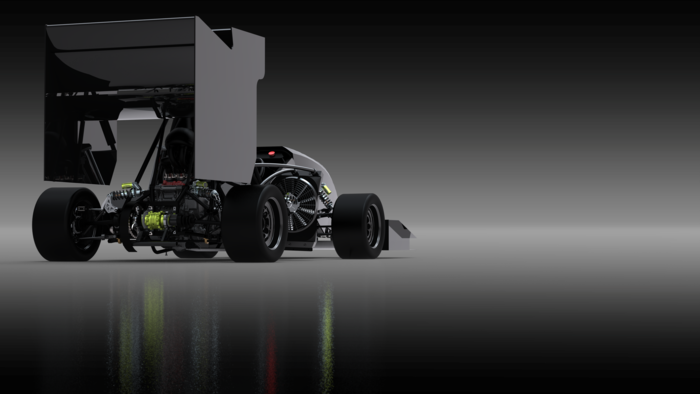
gLike