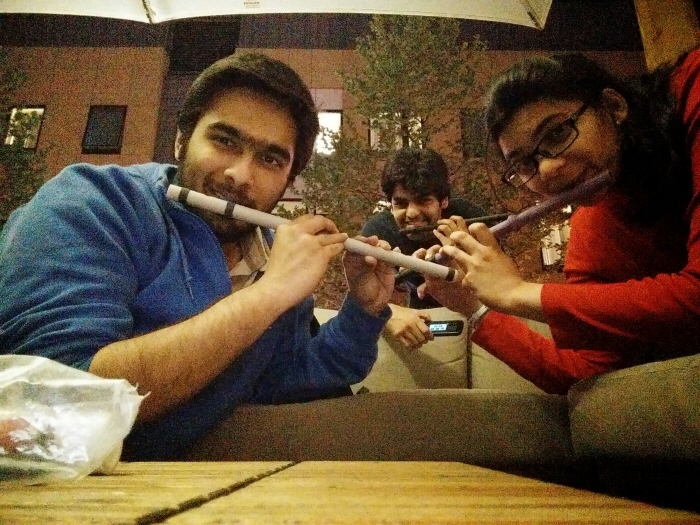
"At first they will ask why we are doing it, later they will ask how we did it - Aspiring Engineers"
Team Indo-Fluters, enjoying the fruits of success.
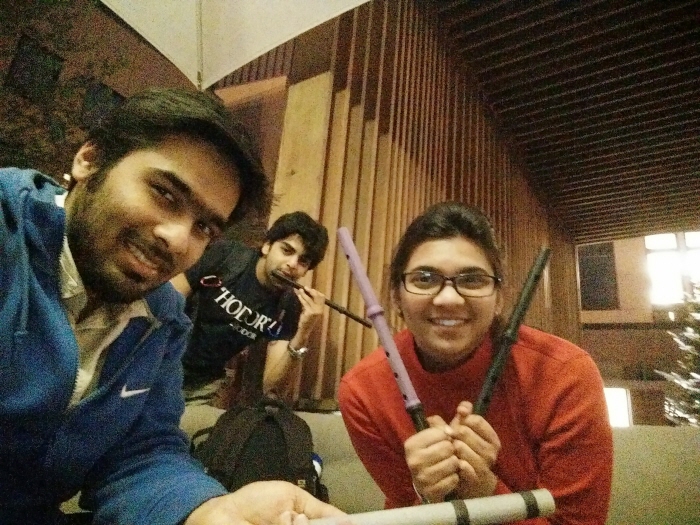
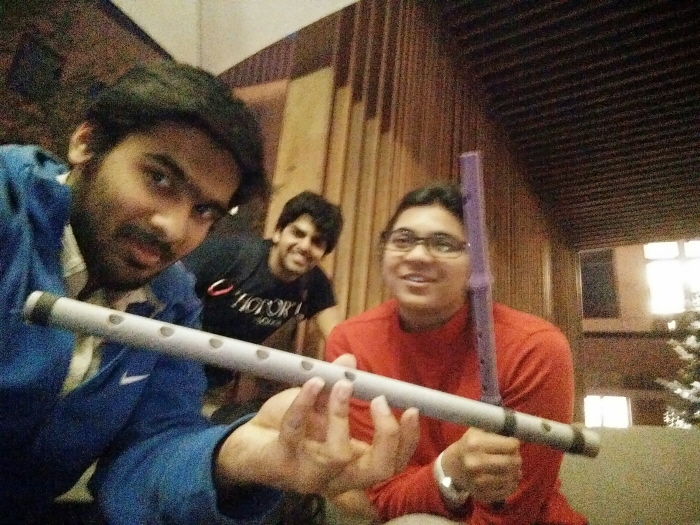
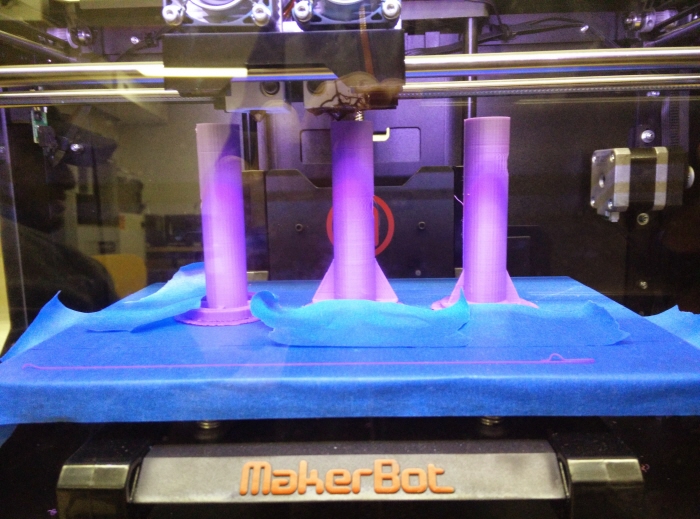
Failure 1: Base warping due to thermal expansion and thermal gradient causing stress which are highly concentrated at the base, uprooting it.
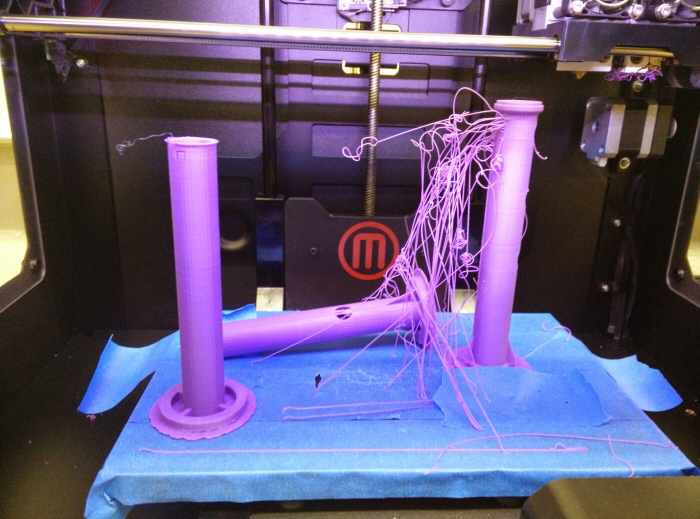
Failure 2: Printing with supports is recommended, but in our case supports were our enemy as they affect the surface smoothness and thus acoustic properties.
Did take a while to learn the art of completion without support
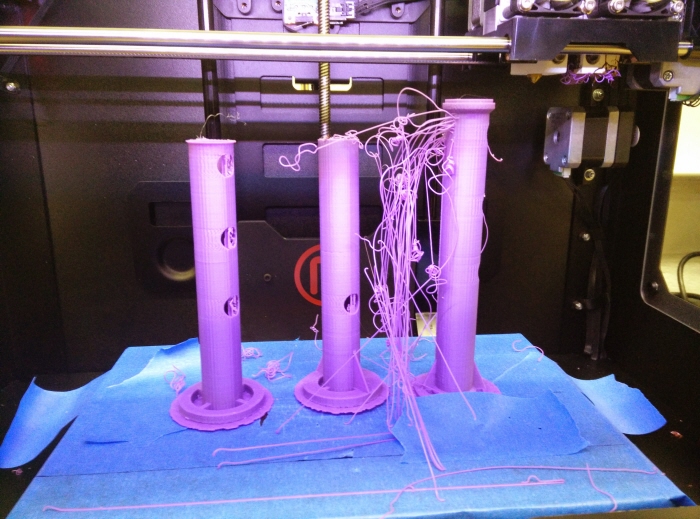
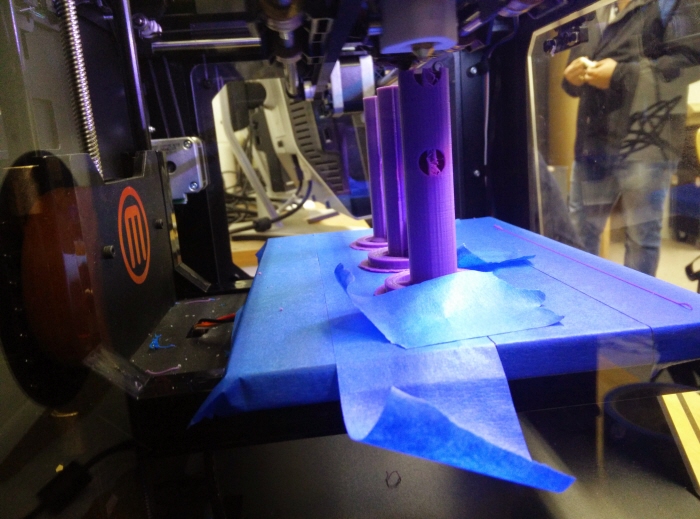
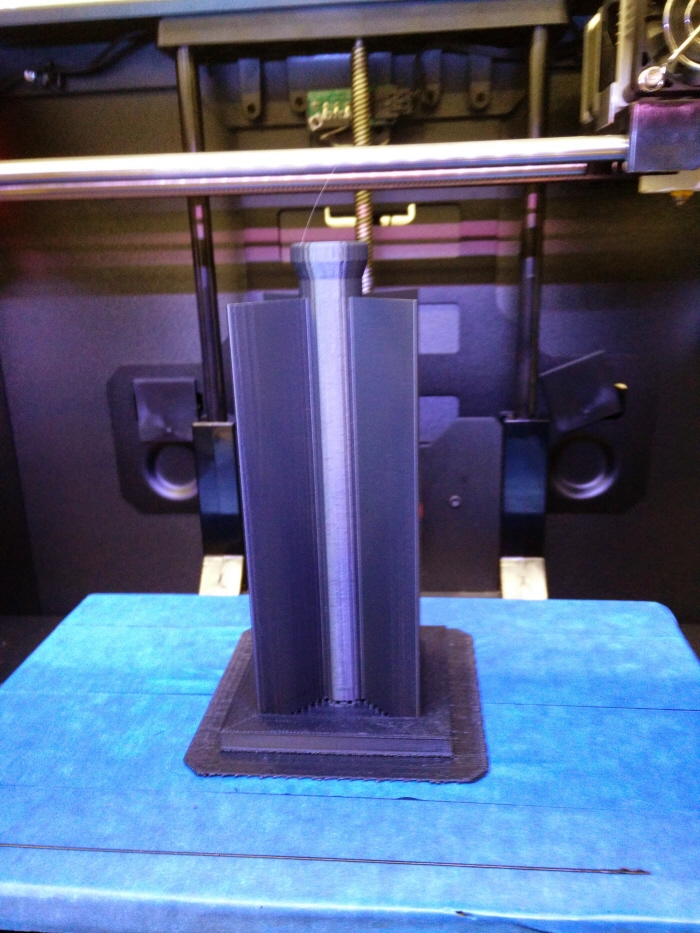
Design creativity: DFMA skills achieved. Sacrificial supports designed within the model. The fins are thin enough to be broken by hand but supportive enough to hold the part while printing
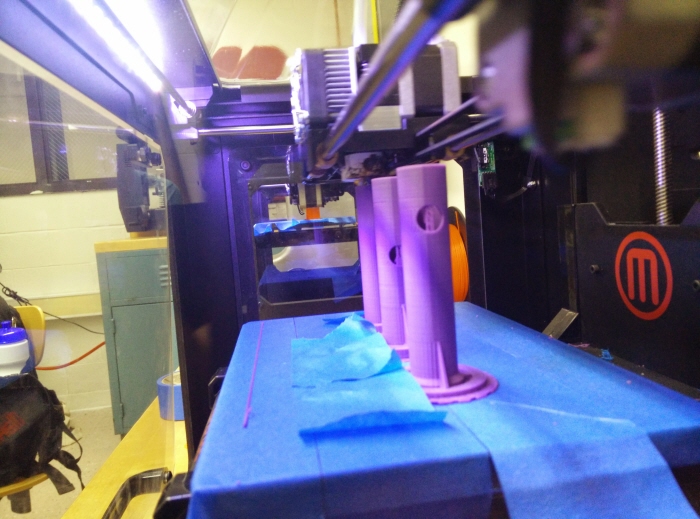
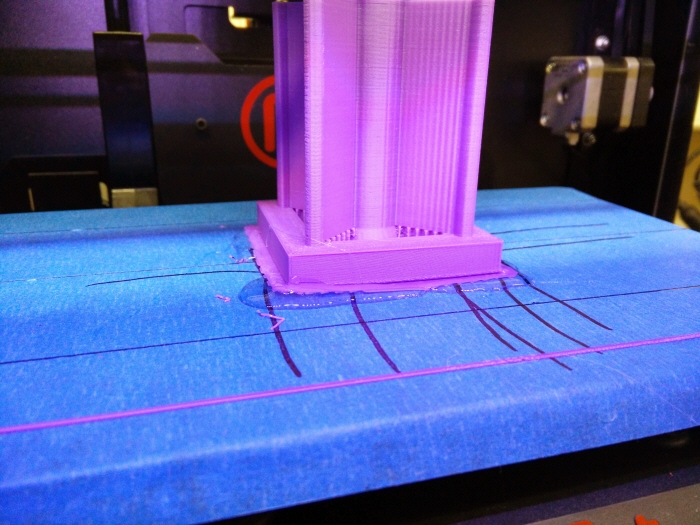
Some layman creativity : When nothing works, Just glue it. Glue works! Simply engineered solutions.
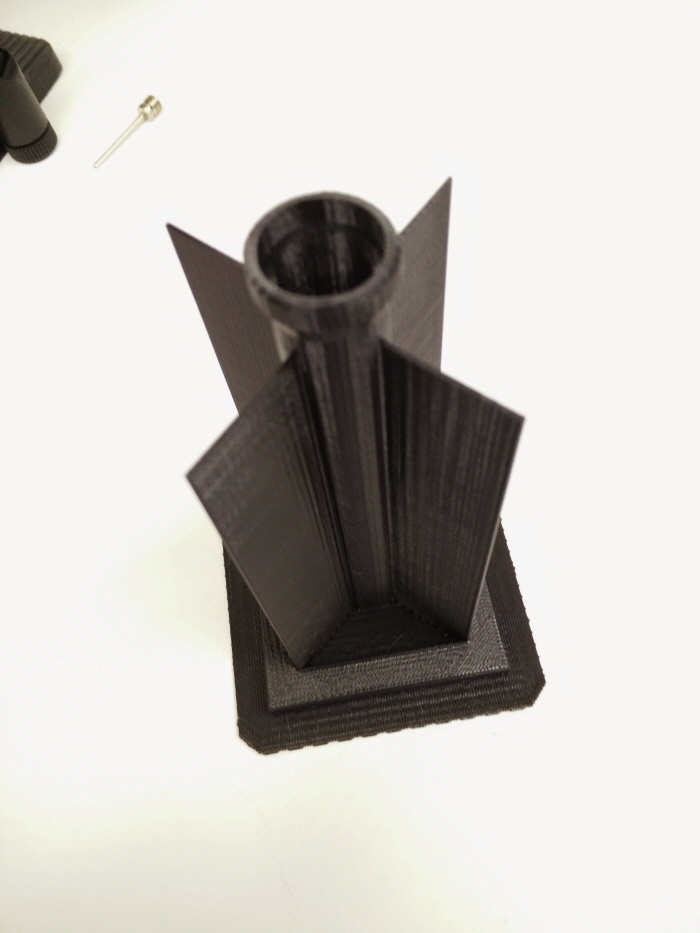
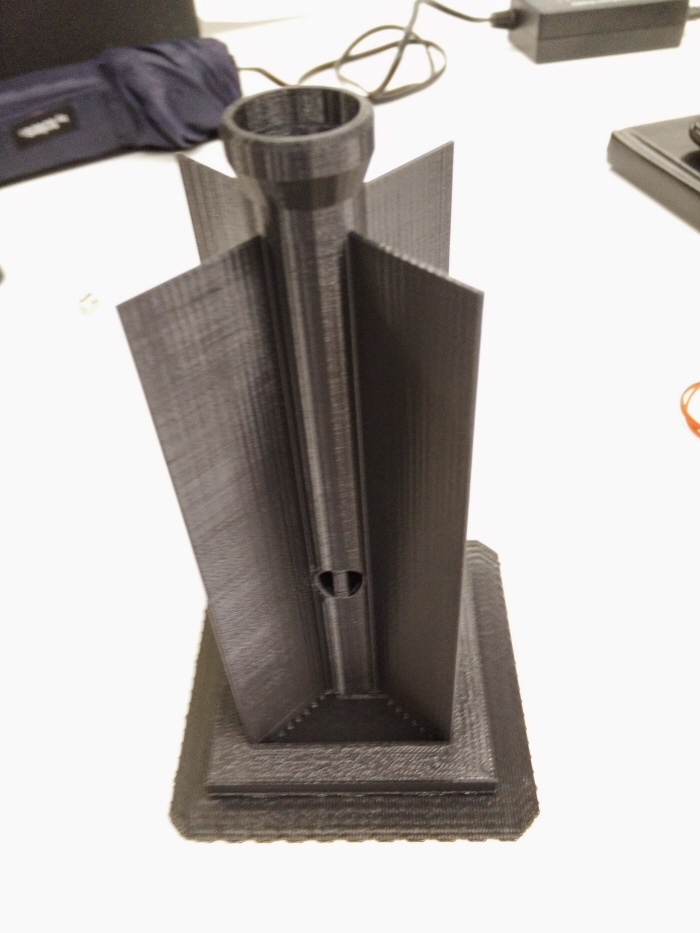
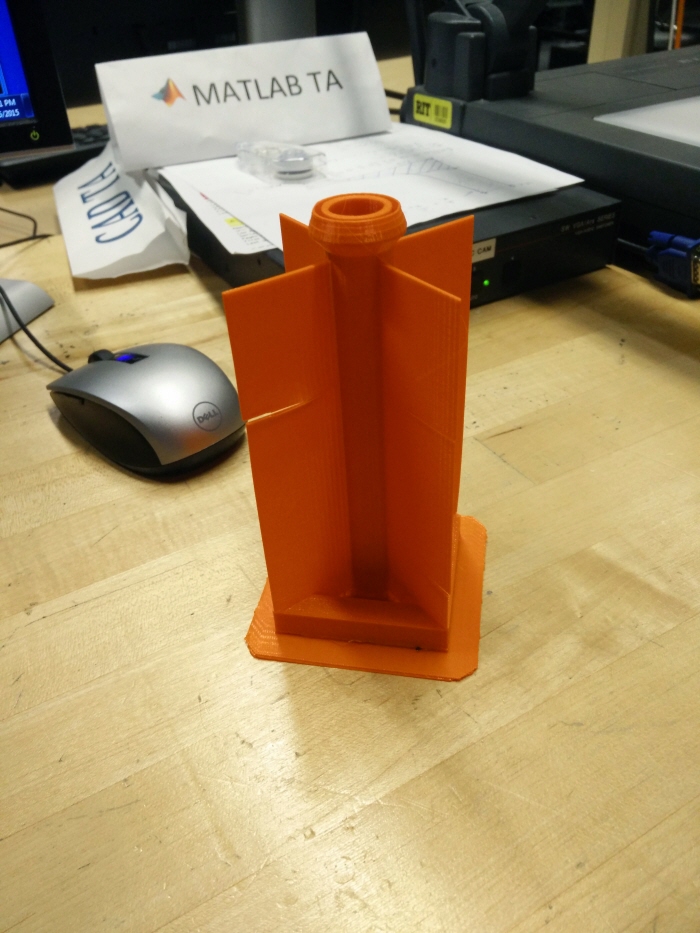
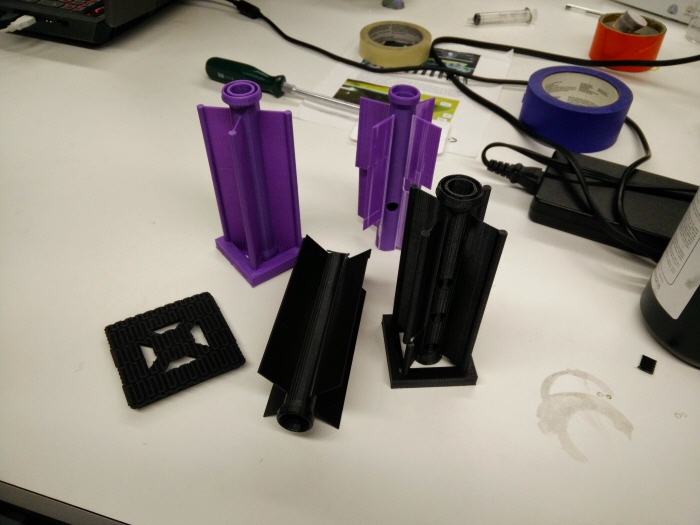
Rockets...No those are not what you think. These are the out come of engineering ingenuity and mechanical acumen. Parts with DFMA features embedded.
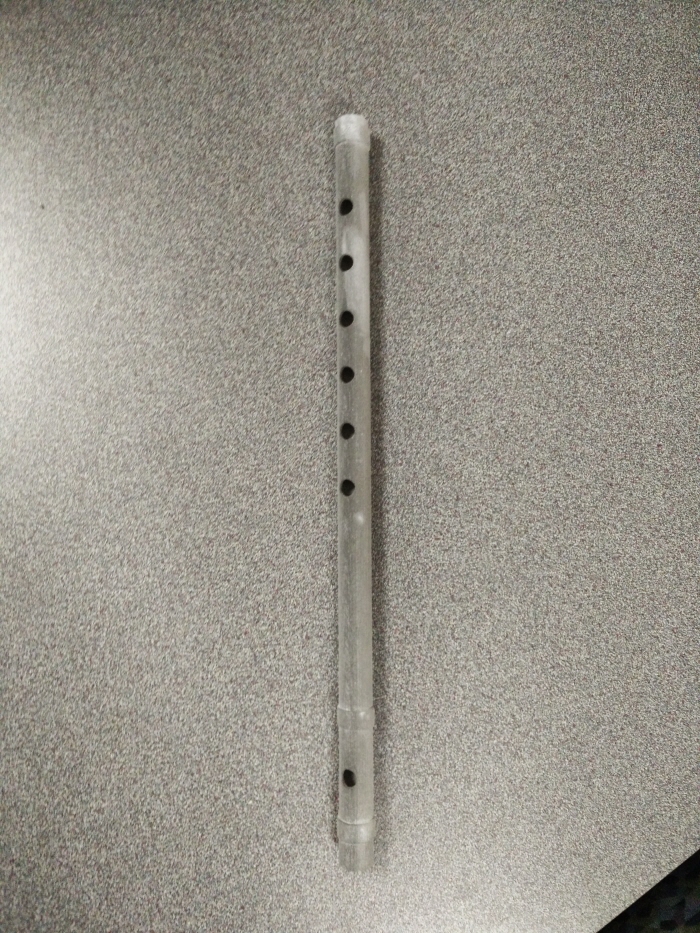
Process 2: Binder-jet technology. Powder + Binder and some layered technology gives you the additive might of geometric freedom.
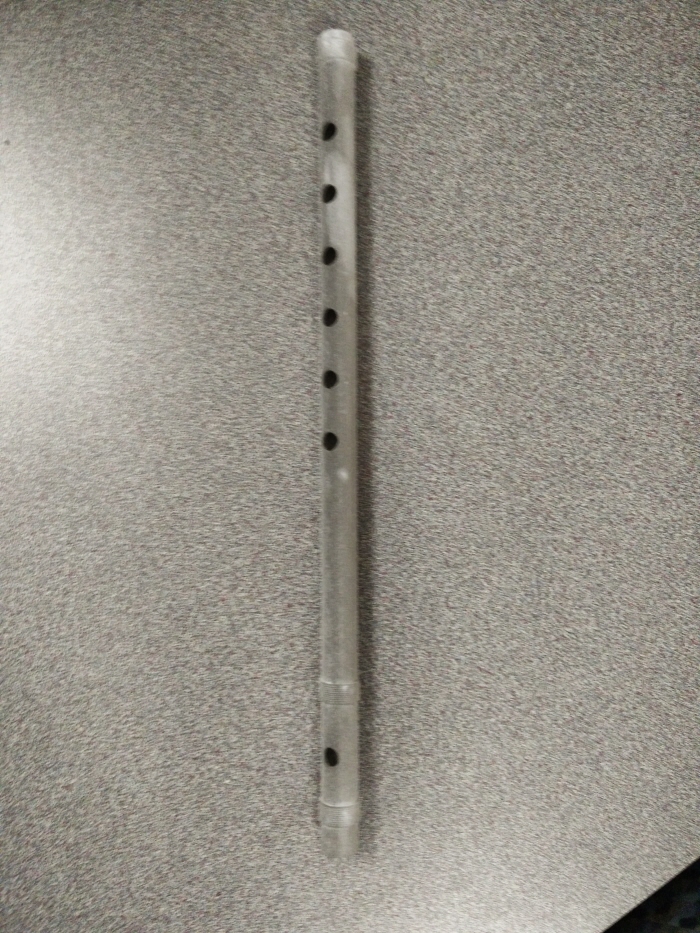
gLike